Monday, July 25th
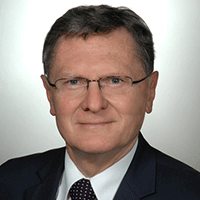
Wieslaw Ostachowicz, Ph.D.
Polish Academy of Sciences
IFFM
Biography: Prof Wieslaw Ostachowicz graduated from Gdansk University of Technology, Poland (receiving the MSc, PhD and DSc degrees in Mechanical Engineering). He has led dynamics research at the Institute of Fluid-Flow Machinery, PAS, for over thirty-five years. Prof Ostachowicz has been visiting professor at the Syracuse University (1980–1981), an expert of UNIDO (United Nations Industrial Development Organization) at the Instituto de Investigaciones Electricas, Cuernavaca, Mexico (1987, 1990), visiting professor at the University of Glasgow, UK (2000–2003) and the Ecole Nationale SupĂ©rieure d’Arts et MĂ©tiers (ENSAM), Paris, France (2017).
Prof Ostachowicz published 435 archival international journal papers, 532 refereed international conference papers, and over 200 technical reports, predominantly in damage detection, structural health monitoring, and advanced signal processing areas. Prof Ostachowicz participated in investigating 24 international research projects as a coordinator, leader of WP (Work Package), or the main contractor, including the European Commission, NATO, EPSRC, US Army. Presently prof Ostachowicz is involved in work (as editor/associate editor) for the following journals: Mechanical Systems and Signal Processing (Elsevier), Structural Health Monitoring (SAGE Publ.), Intelligent Material Systems and Structures (SAGE Publ.), Smart Materials and Structures (IOP Publ.), ASME Jour.-Nondestructive Evaluation, Diagnostics and Prognostics of Engineering Systems; Editorial Board Member, Strain (Wiley), Jour. of Mechanical Engineering Science (SAGE Publ.).
Prof Ostachowicz has received several prestigious awards and distinctions, among others Medal of O.C. Zienkiewicz (2013), Dragon–STAR Innovation Award (1st place) as confirmation of cooperation between Poland (Polish Academy of Sciences) and China (Hohai University and The Hong Kong Polytechnic University), 2015, and SHM Life Achievements Award (sponsored by Boeing Co.), Stanford University, USA (2019). See details in: ORCID 0000-0002-8061-8614
Lecture Title: Nondestructive Assessment of Structural Integrity for Lightweight Structures
Abstract: The paper presents the challenges of non–destructive assessment of structural integrity and failures for lightweight materials. As is well known, such a need results from the necessity to monitor the condition of joints in composite structures and during repairs of damaged structures.
In the initial part of the paper, motivations and research objectives are presented. For the most part, the study shows the inspection methods of composite structure joints. Before joining, the surface assessment methods and the quality assessment methods for structural joints are highlighted. Detailed descriptions of investigated cases are provided. In particular, a study of the surface of polymer reinforced carbon fibres samples (CFRP) with various degradation/contamination is presented.
The investigations of the condition for CFRP bonds are presented next. Particular attention was paid to the issues of various types of degradation, for example, moisture, anti-adhesive agent (release agent), fuel, hydraulic fluid (Skydrol), de-icer, thermal degradation, and improper adhesive curing, errors in bonding, fingerprint. Most of the types mentioned above of degradation pose a severe problem in the aerospace industry (both in manufacturing and service). They are possible sources of weak bonds.
In the central part of the presentation, various methods of NDT (nondestructive testing) and SHM (structural health monitoring) are discussed. In particular, the advantages and disadvantages of the following methods are presented: Electromechanical Impedance, Laser Fluorescence, Laser Vibrometry, Active Thermography and Terahertz Spectroscopy. Effective applications of these methods in testing aircraft components were indicated.
The paper presents the results of research on composite samples as well as small components of aircraft that were degraded due to moisture, initial stresses, thermal influence, icing, and chemical contaminations. Some interesting signal processing techniques were also introduced. Among other things, the effective use of Frechet distance and Mahalanobis distance was indicated. The methods mentioned in the previous sentence proved to be perfect for processing the signal obtained using Laser Doppler Vibrometry.
Tuesday, July 26th
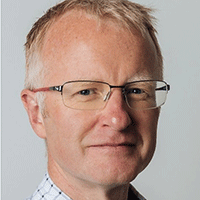
Paul Wilcox, Ph.D.
University of Bristol
Fellow, Alan Turing Institute
Academic Director, UK Research Centre in NDE
Biography: Paul Wilcox is Professor of Dynamics at the University of Bristol, a Fellow of the Alan Turing Institute, and Academic Director of the UK Research Centre in NDE. He received an Engineering Science degree from the University of Oxford (1994) and a PhD from Imperial College London (1998). In 2015 he co-founded Inductosense Ltd., to commercialise inductively-coupled ultrasonic sensors. His research interests include arrays, guided waves, elastodynamic scattering, signal processing and machine learning.
Lecture Title: Applications of Data Science and Machine Learning to Ultrasonic Multi-view Imaging
Abstract: Full Matrix Capture (FMC) and image formation using variants of the Total Focusing Method (TFM) are now routinely available on commercial array controller instruments. However, forming a single image from FMC data only makes use of a small part of the rich information that it contains. Each individual A-scan in an FMC dataset contains superposed responses due to scattering from structural features due to waves that have propagated along multiple ray paths, possibly involving mode conversions and/or reflections. The formation of an image from FMC data assumes a single ray path with responses due to waves propagating on any other ray paths appearing as artefacts. Intuitively, exploiting information from multiple ray paths should improve the detection of defects especially if there is uncertainty about the nature and orientation of potential defects. The natural solution is to form multiple images from the same FMC data using different assumed ray paths; this is termed multi-view imaging.
However, multi-view imaging presents a new challenge of operator information overload, hence data reduction or automation is desirable. A statistical strategy for fusing information from multiple views is presented and shown to yield superior defect detection performance to any individual view. It is also shown how multi-view data can be used in a probabilistic framework for improving characterization of defects once detected.
However, for both detection and characterization, it is first necessary to identify and suppress benign artefacts in multi-view images. This is a task where machine learning can potentially provide an efficient solution and promising initial results will be presented. It is suggested that artefact suppression could be one of the most important and general applications of machine learning for all NDE modalities.
Wednesday, July 27th
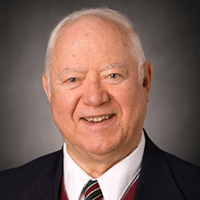
Bernherd Tittmann, Ph.D.
Schell Professor of Engineering, Emeritus
Director of Engineering Nanostructure Characterization Center
Department of Engineering Science and Mechanics
The Pennsylvania State University
Biography: Bernhard R. Tittmann is the Schell Professor Emeritus and the director of the Engineering Nanostructure Characterization Center at the Penn State Department of Engineering Science and Mechanics. Throughout his career, he has also been a visiting professor or lecturer at the Johannes Kepler University in Linz, Austria, and in France at the University of Paris VII and the University of Paris III. He received his B.S. in physics and mathematics from George Washington University in Washington, DC, in 1957 and his Ph.D. in solid state physics from the University of California at Los Angeles, California, in 1965. He has also served on the technical staff in the Materials Mechanics and Physical Electronics Groups at the Science Center of Rockwell International (formerly North American Aviation), before serving as manager of Materials Characterization from 1979 to 1989. He was also the Howard Hughes Fellow in the microwave antenna department of the Hughes Research Lab in Culver City, CA from 1957 to 1962.
Tittmann has been a Fellow of the American Society for Metals (ASM) International, the Acoustical Society of America (ASA), and the Institute of Electrical and Electronics Engineering (IEEE).
Tittmann has been the recipient of many awards, including the Albert Nelson Marquis Lifetime Achievement Award through Marquis Who's Who in 2018 and the IEEE Ultrasonics, Ferroelectrics, and Frequency Control Society’s Distinguished Service Award in 2017. In his career, he has graduated 11 Ph.D. students and 25 M.S. students, been awarded seven patents and three patent disclosures, and has authored or co-authored over 480 publications, including refereed journal publications and proceedings.
Lecture Title: Ultrasonic Transducers for Harsh Environments
Abstract: Ultrasonic transducers play a key role in many strategically important fields in health monitoring and nondestructive testing. Applications that use ultrasonic transducers include the medical, aerospace, railroad, marine, and energy-related industries. The heart of an ultrasonic transducer is the piezoelectric element. Transducers currently used in these industries primarily employ PZT5-H as the piezoelectric element for ultrasound transmission and detection. This material has a Curie–Weiss temperature that limits its use to about 210 °C. Some industrial applications require much higher temperatures, i.e., 350–1000 °C. Examples are heat engines, steam generators, heat exchangers, steam pipes, deep geological exploration, nuclear reactors, steel industries and more.
The goal of this presentation is to survey and review piezoelectric elements for use in high-temperature and some radiation environments for the ultimate purpose of structural health monitoring (SHM), non-destructive evaluation (NDE), and non-destructive material characterization (NDMC). The survey comprises the following categories:
- High-temperature applications with single crystals;
- Thick-film ceramics, and composite ceramics;
- Sol–gel and spray-on transducers.
In the latter category, recent breakthroughs in the doping of certain ceramics have produced exciting new piezoelectric composites having substantial increases in the Curie temperatures. In each category, the known characteristics are listed, and examples are given of performance in harsh environments.