Plenary I: Understanding the Complexities of Sealing in a New Energy Era
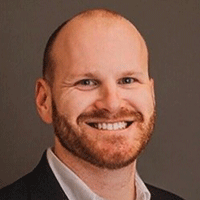
Robbie Riggs
President & CEO
Teadit North America, TX, United States
Abstract: This presentation explores the importance of managing fugitive emissions, with a focus on hydrogen as a clean energy source. While sealing can have many challenges in several applications, it is particularly important to ensure that when sealing a small molecule such as hydrogen, these challenges are explored and addressed.
Fugitive emissions will first be explored including definition and importance. What we currently know about fugitive emissions and controlling them will also be explained in detail. In our current energy climate, it is important to also discuss alternative energy sources in combination with fugitive emissions, to ensure a comprehensive understanding of a new energy era.
While hydrogen does not produce CO2 during energy conversion, leaks would pose safety and environmental risks. Despite being the lightest and most abundant element in the universe, hydrogen has a surprisingly high global warming potential when it leaks into the atmosphere. Even small amounts of hydrogen can contribute to the greenhouse effect, which underscores the importance of stringent containment measures. This presentation will discuss the challenges of sealing hydrogen, including its small molecular size, high permeability, and the difficulty of detecting leaks. The session will also address the complexities involved in sealing hydrogen in various applications, especially electrolysers.
Safety implications of hydrogen leaks is another point that will be addressed, as hydrogen’s low density causes it to rise, posing a significant risk in confined spaces. Hydrogen is also difficult to detect, as it lacks odor and color.
Traditional sealing materials and methods often fall short when dealing with hydrogen, making it essential to develop specialized solutions. In conclusion, the safe and effective use of hydrogen as a clean energy source depends on specialized sealing expertise, in combination with a focus on reducing fugitive emissions from other sources. Ensuring that hydrogen is properly contained, and leaks are minimized is crucial for realizing its full potential in a sustainable energy future.
Biography: Robbie Riggs serves as the President and CEO of Teadit North America, located in Pasadena, TX. With a robust background as a degreed engineer, he has over 20 years of experience in the oil & gas and chemical process industries. He holds several patents for innovative sealing solutions, reflecting his commitment to addressing complex industry challenges. Over the past six years, Robbie has been a driving force behind the company's growth, leading strategic initiatives that have enhanced Teadit's market position. Robbie's leadership emphasizes continuous improvement and collaboration, fostering an environment that encourages creativity and innovation. His forward-thinking approach has introduced new technologies and processes, further solidifying Teadit's reputation for excellence. Beyond his role at Teadit, Robbie is active in industry associations, regularly participating in conferences and forums to share his expertise and stay updated on emerging trends. He is also dedicated to mentoring the next generation of engineers, helping shape the future of the industry.
Plenary II: Exploring the behavior of Expanded PTFE Gasket Material Performance Variation Comparing Solid to Jointed Constructions including Hot Blowout Thermal Cycling Testing
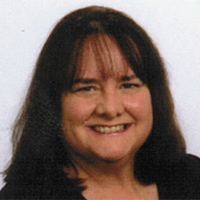
Anita Bausman
P.E. Senior Applications Engineer
VSP Technologies
Kingsport, TN, United States
Polytetrafluoroethylene (PTFE) is an excellent gasket material. Expanded PTFE (ePTFE) achieves better mechanical performance compared to plain PTFE by a highly fibrillated microstructure. However, between the fibers of the ePTFE, there are air voids. To achieve superior sealing, the microstructure must be adequately compressed to close these voids and reduce permeation leakage through the material's microstructure. During this compression, the ePTFE dimensions shrink in contrast to most PTFE sheet materials that radially expand when compressed. This ePTFE behavior is problematic where a gasket with a joint is needed, for example on industrial column body flanges larger than available ePTFE sheets. The ASTM WK61856 Hot Blowout Thermal Cycling (HOBTC) test is in the final stages of ASTM approval. This test has evolved into an excellent judge of PTFE-based sheet materials’ mechanical performance. A working understanding of the HOBTC test results helps an end user select the right PTFE material for their application and optimize plant procedures. ePTFE sheet materials are currently the leading competitors of the PTFE group as far as mechanical performance is concerned. However, the microstructure that gives ePTFE its mechanical advantage over conventional PTFE also poses problems where a jointed construction is needed. Care must be taken to make a leak-free ePTFE joint on such gaskets. Industry experience with the common dovetail joint has been poor using ePTFE materials. However, joints are sometimes needed. In ASME PVP2024-122810, the authors investigated the leakage and mechanical performance of ePTFEs as solid rings without joints, industry-standard dovetail jointed rings, and Engineered Interference Tortuous Path (EITP) jointed rings. Leakage performance was evaluated according to the EN13555 leakage test at room temperature. This presentation reviews the use of HOBTC test results to evaluate PTFE-type sheet gaskets and extends ASME PVP2024-122810 by completing the HOBTC testing on solid and selected jointed ePTFE ring gaskets. Lab tests were performed on an amtec TEMES fl.ai1 test fixture at the authors’ company.
Biography: Anita Bausman is a 1985 graduate of the Georgia Institute of Technology and is a registered Professional Engineer in TN, VA, PA, and SC. She spent the first two decades of her career with Eastman Chemical Company in a variety of plant and piping engineering roles, most notably serving as the Gasket and Piping subject matter expert. Anita joined VSP Technologies in 2009 and is a Senior Applications Engineer working out of VSP’s Tennessee Regional Office in Kingsport. She currently serves on the ASME RTP Design Subcommittee (low-pressure nonmetallic vessels) and ASME NPPS Design Task Group (non-metallic pressure piping). Anita is a member of the ASTM F03 technical committee on gaskets and was heavily involved in the development of the Hot Blowout Thermal Cycling test for PTFE gasket materials. Ms. Bausman has been a frequent contributor to ASME technical organizations and conferences and has authored several papers for the ASME Pressure Vessel & Piping (PVP) conferences and presentations for the ASME Bolted Joint Reliability Symposiums (BJRS).
Workshop: On Flange Design Based on Tightness: A Graphical Method
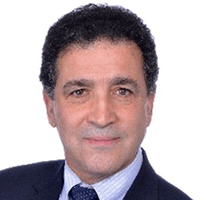
Hakim A. Bouzid
Ph.D, ASME Fellow
Professor, Ecole de Technologie Supérieure
Montreal, Qc, Canada
Abstract: This workshop covers the use of a graphical method to design bolted flange connections based on the new gasket constants Gb, a and Gs. The workshop starts by describing the main changes that are being adopted by the ASME SWG on Bolted Flange Connection. The new rules parallel those currently in use in Appendix 2 method A based on m & y and method B based on new gasket constants Gb, a and Gs, the consideration given to gasket degradation and relaxation, The tightness concept and its relation to leakage, the importance of tightness and gasket stress, external Loads, gasket temperature limits, assembly efficiency and bolt spacing are to name a few. It then explains the basic concept of tightness and introduced the tightness classes and their corresponding level of leakage. The ROTT ROom Temperature Tightness test and the procedure to obtain the new gasket constant Gb, a and Gs are briefly described. The correlation between leak rates of gases and liquids follows. Examples are given to correlate between helium used as a reference gas and other gases and liquids, gasket prorating and the correspondence between leakage and tightness classes and vis-versa. A new bolt load design calculation method based on a graphical approach is treated with examples on different flange sizes, fluid media and operating conditions. The use of the new gasket constants to design bolted flange connections based on a tightness criterion will therefore be made simple and accessible to the designer, end user and application engineer.
Biography: Dr. Hakim Bouzid is a full professor at Ecole de Technologie Supérieure of Montreal Canada. He graduated from mechanical engineering Department of Nottingham University, UK, 1981. He holds a master Degree in Tribology from Leeds University, UK in 1982. He has a Ph.D in bolted joints received from École Polytechnique, Montreal, Canada, 1995. He worked in the nuclear industries for 8 years specializing in pressure vessels and piping before joining the Tightness Testing Research Laboratory at Ecole Polytechnique in 1990 as a research scientist. In 2000, he became a professor at Ecole de Technologie Superieure in Montreal. He is currently the director the Static and Dynamic Sealing Laboratory of ÉTS. Prof. Bouzid has authored or co-authored over 250 technical papers on different subjects including stress analysis, bolted joints, valves, polymers and biomechanics.
Dr. Bouzid is a fellow of ASME. He is a member of the Pressure Vessel ad Piping Division Executive committee. He served as a member of the Pressure Vessel Research Council, ASME subworking Group on Bolted Flange Connections, ASME PCC-1 and ASTM F03 committee on gaskets.