Keynote
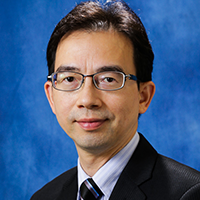
Wei-Hsin Liao
The Chinese University of Hong Kong (Hong Kong, China)
Title: Vibration, Energy Harvesting, Human Motion
Abstract: By utilizing adaptive features, smart materials can be built as actuators and sensors. They were used as intelligent elements for vibration control of structures. Besides passive approach, active, semi-active, and active-passive hybrid vibration control have been extensively studied. For vibration control, applications to hard disk drives using piezoelectric actuators with passive damping, semi-active train suspension systems utilized controllable MR dampers will be shown. On the other hand, energy can be harvested from vibration and human motion. Piezoelectric and electromagnetic power generators were used to transform the mechanical energy from vibration and human motion into electrical energy. An energy flow was proposed with detailed analysis to clarify and illustrate each branch of the energy flow in piezoelectric energy harvesting systems. An equivalent impedance network was proposed and investigated. Since there is a large amount of kinetic energy in the human body during activities, capturing human motion and converting it into electricity is envisaged to render promising prospects for sustainably powering wearables and fulfilling the continuous working requirement of IoT applications. Aimed at scavenging the kinetic energy of the human joints, various energy harvesters have been designed and investigated. Besides, robotic exoskeletons and smart ankle-foot prostheses that can assist people with impaired mobility have been developed. Our related work will be presented.
Biography: Wei-Hsin Liao received his Ph.D. degree in mechanical engineering from The Pennsylvania State University, University Park, PA, USA. Since 1997, Dr. Liao has been with The Chinese University of Hong Kong, where he is currently a Professor and the Chairman of the Department of Mechanical and Automation Engineering. His research has led to publications of over 280 papers in international journals and conference proceedings, 19 granted patents. As the General Chair, he organized the 20th International Conference on Adaptive Structures and Technologies (ICAST 2009). He was the Conference Chair for the Active and Passive Smart Structures and Integrated Systems, SPIE Smart Structures/NDE in 2014 and 2015. He received the T A Stewart-Dyer/F H Trevithick Prize 2005, awarded by the Institution of Mechanical Engineers, the ASME Best Paper Awards in Structures (2008), Mechanics and Material Systems (2017). Dr. Liao is the recipient of the SPIE 2018 SSM Lifetime Achievement Award, and ASME 2020 Adaptive Structures and Material Systems Award. He currently serves as an Associate Editor for the Journal of Intelligent Material Systems and Structures, as well as Smart Materials and Structures. Dr. Liao is a Fellow of the American Society of Mechanical Engineers, the Institute of Physics, and the Hong Kong Institution of Engineers.
Invited Speakers
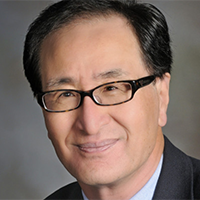
Title: Energy Harvesting for Wireless IoT Devices
Abstract: IoT (Internet of Things) devices will be able to provide innovative services and solutions in the realms of such as smart homes, smart cities, and smart factories. It is envisioned that trillions of IoT devices such as sensors, cameras, and wearables will be connected to the Internet, forming a massive IoT ecosystem. Further, low power wireless technologies such as Bluetooth, Wi-Fi, ZigBee, Cellular, and RFID enable IoT devices to connect with each other over wireless links.
A major design issue for wireless IoT is autonomous power, and energy harvesting is a promising solution. Energy harvested from ambient sources aims to recharge the battery of a wireless IoT device or even remove the battery perpetually. Typical energy harvesting sources include solar, thermal, kinetic, and radio frequency. The operating environment of ambient energy sources changes and the energy level of typical ambient energy sources is low. It poses major design issues for energy harvesting circuits. This talk covers design issues of energy harvesting circuits for various energy sources and major design schemes to address the problems. It also covers recent advances and research issues in energy harvesting circuits built on SoC (System on Chip).
Biography: Dong S. Ha received a B.S. degree in electrical engineering from Seoul National University, Korea, and M.S. and Ph.D. degrees in electrical and computer engineering from the University of Iowa. Since Fall 1986, he has been a faculty member of the Department of Electrical and Computer Engineering, Virginia Tech. He is Founding Director of the Multifunctional Integrated Circuits and Systems (MICS) group with four faculty members and a member of Center for Energy Harvesting Materials and Systems (CEHMS) of Virginia Tech. He specializes in low-power analog RF IC design. His research interests include energy harvesting circuits and systems, high temperature RF ICs, and wireless sensor nodes with machine learning. He is a Fellow of the IEEE.

Title: Structure, Stiffness, and Multi-Stability Design in Compliant/Flexible Mechanisms
Abstract: Compliant mechanisms utilize bending or torsion of flexible beams to transfer motion, force or energy, and have received increasing attentions over the last two decades due to their merits in terms of reduced cost and increased performance. In this talk, we will present some recent work on structure, stiffness, and multi-stability design in compliant/flexible mechanisms. A structure design method is firstly discussed, which is based on the position-space that can be identified by the screw theory. This structure design method can complement other existing design methods such as FACT, and can be used to produce compact configuration, reduced parasitic motions and/or other purposeful reconfigured designs. Then, a stiffness design method is presented, which will be demonstrated by controlling the internal axial load and using tensural-compresual general beams. Finally, a multi-stability design method is reported by designing the elastic potential energy or magnetic potential energy at multiple local minimums, and a self-folding chain for minimum invasive surgery is elaborated.
Biography: Dr. Guangbo Hao is a Senior Lecturer at University College Cork (UCC), and also an academic associate in Tyndall National Institute, Ireland. He is leading the CoMAR research group. His current research interests focus on design of compliant mechanisms and robotics and their applications in precision engineering, energy harvesting and biomedical devices. His research works were indicated by 2 filed patents, 130 peer-reviewed publications and 20 invited talks (3 keynote/plenary), and by successfully securing research grants from EU, Ireland, and China. He is an elected member of the ASME Mechanisms and Robotics Committee. He is serving as an Associate Editor of ASME Journal of Mechanisms and Robotics, the Editor-in-Chief of the IFToMM affiliated journal: Mechanical Sciences (MS), and an overseas editorial board member of Chinese Journal of Mechanical Engineering (CJME). He acted as the Chair of the 2016 and 2018 ASME IDETC/CIE Compliant Mechanism Symposiums, an Associate Editor of 2017-2019 IEEE IROS conferences, and a Program Chair in the 2018 4th IEEE/IFToMM International conference on Reconfigurable Mechanisms and Robots. He received some prizes including the solo winner of 2017 ASME Compliant Mechanisms Award in Application, the joint winner of the 2018 ASME Compliant Mechanisms Award, the winner of the Young Engineers Research Paper Prize 2012 (3rd Prize) presented by IMechE and Engineers Ireland, the Royal Irish Academy Charlemont Award for 2015.
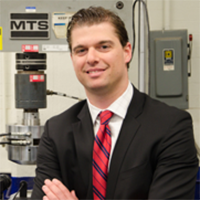
Title: An Internet of Things Approach for Dynamic and Data-Driven Remaining Useful Life Predictions
Abstract: In prognostic health management multiple gaps have been identified when making estimations or predictions of the current state and the associated remaining useful life (RUL), many of which are associated with the acquisition, handling and use of available sensing information. What is understood currently is that prognostics must account for the stochastic and coupled, also often nonlinear, effects that govern e.g. the progressive failure process structural applications. Practically data acquired during experimental testing and is used to either fit prognostic parameters or perform statistical inference is typically subject to a high amount of variance. Consequently, monitoring of the progressive failure is characterized by high uncertainty making physics-based models either computationally expensive for live prediction or specialized to account for specific damage occurring among This is especially true in the case that the convolution levels make it difficult to discriminate between noise and actual damage. To address signal convolution and increase the capability to identify evolving states of damage, data mining is required to discriminate between signals that allude to noise and signals that are most likely to be attributed to damage. Additionally, when training methodologies that are not physics-based, data management becomes increasingly difficult. To address therefore such data management issues, a data-driven, distributed and dynamically updated methodology of computing could provide significant advantages to diagnostics and prognostics by objectively dealing with system noise and enhancing prediction capabilities. Such approaches intend to filter, aggregate and consolidate data both for training as well as predictions that also account for the volume, veracity and velocity of incoming data streams related to degradation.
To this aim, a novel Internet of Things (IoT) approach will be presented in this talk. At the core of the approach is the creation of a NoSQL database which is implemented to provide dynamic data transfer from the different components of the approach including the Edge, Fog, and Cloud layers. Specifically, the Edge is responsible for collecting raw data signals and is the closest layer to data collection. Key algorithms to cluster, classify, and filter signals are implemented at the Fog to create an efficient stream of useful data to the Cloud. From there, the processed data is sent to the Cloud for the retraining of algorithms and storage of historical data. These three layers provide the ability to limit human intervention and create a self-correcting knowledge-based system through back propagation.
In the implementation of the approach discussed in this talk, sensing data include inputs from Nondestructive Evaluation (NDE) methods including Acoustic Emission and Digital Image Correlation Data. This information is coupled with mechanical testing data obtained directly by the testing equipment. To demonstrate the capabilities of the approach, results from crack growth monitoring in metallic specimens and components is presented. At first and to validate the approach, compact-tension specimens of aluminum are used in accordance with standardized testing procedures to create a verifiable datasets of crack growth data based on the sensing methods selected in both monotonic and cyclic loading conditions. Such data is used to train a support vector machine alongside a Hidden Markov Chain model that provide the classification of the data into a number of representative states in accordance with the crack growth process. This classification and mechanical test data is then used as inputs to an adaptive neuro-fuzzy network that produces the RUL predictions. To expand the proposed approach beyond standardized test geometries results and apply it to e.g. structural components subjected to more complex loading conditions, notes are presented to demonstrate the capability to adapt and implement the approach in Structural Health Monitoring Applications.
Keywords: Prognostic Health Management, Internet of Things, Data Processing, Database Management, Edge Analytics, Remaining Useful Life predictions
Students contributing to this work: Sarah Malik, Rakeen Rouf and Krzysztof Mazur
Biography: Dr. Antonios Kontsos is an Associate Professor in the Mechanical Engineering & Mechanics Department at Drexel University where he is currently the Director of the Theoretical and Applied Mechanics Group (TAMG). He received his undergraduate 5-year Diploma (2002) in Mechanical Engineering & Aeronautics from University of Patras (Greece), and his M.S (2005) and Ph.D. (2007) degrees in Mechanical Engineering & Materials Science from Rice University (Houston, TX). Before joining Drexel in 2009, Dr. Kontsos held a post-doc position at the Center for Mechanics of Solids, Structures and Materials in the Aerospace Engineering & Engineering Mechanics Department at the University of Texas at Austin (Austin, TX). Dr. Kontsos’s primary research interest is in the theoretical, experimental and computational investigation of the mechanical behavior of materials with emphasis on understanding microstructure-properties-behavior evolving relationships.
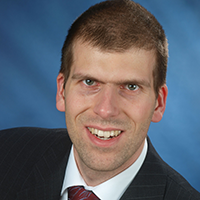
Title: Functionally graded materials by additive manufacturing – From conventional to shape memory alloys
Abstract: Additive manufacturing (AM) allows for realization of components of unprecedented geometrical complexity. Due to the principle of layer-wise manufacturing enabled only by a sliced design file, topologically optimized components can be easily manufactured. Most commonly employed techniques comprise laser- and electron beam powder bed fusion (L-PBF and E-PBF) as well as laser metal deposition (DED). All techniques are characterized by very characteristic features in a very similar way: relatively small melt pools, rapid solidification and intrinsic heat treatment. Thus, all these techniques allow to establish unique microstructures, provided that apt process parameters are employed. As these process parameters in principle can be adjusted on purpose in given volumes, realization of microstructurally and functionally graded components is feasible.
The present paper presents pathways towards tailoring local properties. Focus will be on both conventional and shape memory alloys (SMAs) as well as conditions combining these two different materials within one structure. Results shown will highlight prospects and challenges by detailing microstructure evolution, process induced defect structures, adequate post treatments and eventually mechanical and functional properties.
Biography: Dr.-Ing. Thomas Niendorf is Full Professor at the Institute of Materials Engineering at University of Kassel (Germany) since October 2015. Dr. Niendorf studied Mechanical Engineering at University of Paderborn (Germany). In 2010 he did his doctorate. Dr. Niendorf’s research interests are in the interrelationships of process, microstructure, mechanical properties and reliability of metallic materials. Analysis of residual stresses, microstructure evolution and fatigue performance are key aspects of research projects conducted. Materials in focus are steels, aluminum alloys, high-temperature materials, shape memory alloys as well as hybrid materials.
Research activities in the field of additive manufacturing (AM) comprise powder bed techniques (L-PBF and E-PBF) as well as laser metal deposition. Realization of microstructurally graded samples for improved functionality as well as thorough characterization of integrity and reliability of AM components are Dr. Niendorf’s actual fields of research in AM. Dr. Niendorf published more than 150 peer-reviewed papers in renowned journals. Furthermore, he holds several patents and has been invited speaker in many conferences. He has been scientific board member and session organizer in several European conferences focusing on AM. For his young career achievements he received several distinguished awards, e.g. the Heinz Maier-Leibnitz-Award by German Research Foundation.
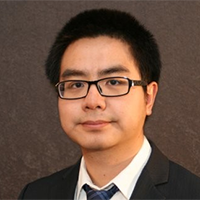
Title: Combinatorial Development of Copper Based SMA
Abstract: Copper based SMAs offer higher thermal conductivity and lower cost than the most popular Ni-Ti based SMAs, but suffer from brittleness and low stress to reach super-elastic plateau. Cu-Al-Mn based SMA was reported to exhibit excellent cold workability if its parent A2 phase is disordered, which can be achieved by tuning its composition, such as by limiting its aluminium content to <16 at.%. Unfortunately, such tweaking of compositions also results in shifting of phase transformation temperature outside of the desired working temperature range. A comprehensive compositions optimization effort was carried to identify the fourth and fifth elements allowing the SMA to exhibit reasonable ductility while maintain a good phase transformation characteristic. The effort used combinatorial arc melting technique to rapidly synthesize hundreds of small bulk alloy samples. Bulk sample is preferred over thin film sample despite the fact that the throughput of combinatorial thin film method is much higher. This preference is due to the difficulty in reliably characterizing phase transformation behaviour and crystal structures of thin film. The obtained bulk samples are in the form of a small button weighing about 1-2 gram. These buttons were batch-sealed into quartz ampules and subjected to heat treatment involving solution treatment and quenching. Subsequent characterizations include x-ray for lattice parameters and phase identification, hardness testing, ultrasound elastic module measurement, and thermal imaging screening for phase transformation. The down-selected candidates were further studied using the conventional metallurgical method such as drop casting, DSC, x-ray, and flexural strength measurement using 3-point bending technique. The final composition was also thermal-mechanically treated to refine grain sizes and to encourage the desired texture. In this talk, detailed experimental work will be presented and possible mechanism leading to the disordered A2 phase will be discussed.
Biography: Dr. Ouyang joined Ames Laboratory (a U.S. Department of Energy National Laboratory) as an Assistant Scientist in 2019. Before that, he was a post-doc researcher at Iowa State University (2016-2019). Dr. Ouyang’s current research focuses on ferroic materials and high temperature structural materials. His current research projects include combinatorial synthesis and characterization of shape memory alloys and elastocaloric materials, high entropy alloys for high temperature applications, and Fe-Si based soft magnetic materials for motor and power electronics. Dr. Ouyang has extensive experience in shape memory alloys, soft magnetic materials, high temperature alloys and ceramics, and materials processing and characterization. He has 18 papers published on peer review journals and 5 pending patents.
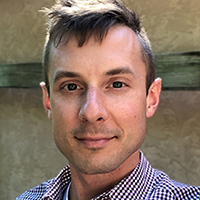
Title: Smart Mechanical Matter
Abstract: An accelerating attention to flexible electronic materials and devices has opened doors for electronics and machines that seamlessly engage with humans via soft and compliant interfaces, impacting applications of healthcare, medicine, personal electronics, manufacturing, and more. Yet, the attention has largely focused on elementary functional devices such as strain sensors, whereas modern electronics rely on digital logic and determine behavior on the basis of sophisticated intelligence and controllers. This talk will highlight emergent research that creates a bridge between the operation of conventional integrated circuits and advances in soft, conductive materials via a new class of smart mechanical matter. By devising a tangible analogy between Boolean logic and modal behaviors of conductive, mechanical metamaterials, logic gating behavior is cultivated according to mechanical stress application on the metamaterials. This in turn facilitates digital computation and control in response to the stress. The talk summarizes computational and experimental efforts to explore this new opportunity for mechanical metamaterials to directly govern operation of digital controllers. The talk concludes with a detailed vision that synthesizes new and future advances in mechanics, materials, biology, chemistry, and computer science to realize soft, autonomous machines that may independently navigate our world to assist in applications as diverse as ecological reporting, wound healing, assisted living, vehicle safety, and much more.
Biography: Ryan L. Harne is the James F. Will Career Development Associate Professor in the Department of Mechanical Engineering at The Pennsylvania State University where he directs the Laboratory of Sound and Vibration Research. Ryan earned his Ph.D. degree in Mechanical Engineering at Virginia Tech in 2012. From 2012 to 2015, Ryan was a Research Fellow at the University of Michigan. His research expertise spans mechanics, dynamics, vibrations, materials, and manufacturing. He has led research efforts yielding 80 publications, 2 patents, 1 book, 25 student awards, and 1 startup company. Ryan is active in the ASME, ASA, and SPIE in multiple organizational roles. Ryan's contributions to science and engineering have been acknowledged by being recipient of the 2020 ASME CD Mote Jr. Early Career Award, the 2019 ASME Gary Anderson Early Achievement Award, the 2018 National Science Foundation CAREER Award, the 2017 ASME Best Paper Award in Structures and Structural Dynamics, the 2016 ASME Haythornthwaite Young Investigator Award, and the 2011 ASA Royster Award. He currently serves as an Associate Editor for ASME Journal of Vibrations and Acoustics and for the The Journal of the Acoustical Society of America, Proceedings of Meetings on Acoustics.
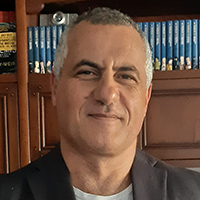
Title: Status and perspectives of commercial aircraft morphing
Authors: Antonio Concilio (speaker) and Salvatore Ameduri
Abstract: In a previous paper, the authors dealt with the current showstoppers for morphing systems and a number of reasons that have inhibited their commercial applicability. In this work, the authors would like to express a critical vision of the current status of the proposed architectures and the needs that should be accomplished to make them viable for installation on-board of commercial aircraft. The distinction is essential because military and civil issues and necessities are very different, and both the solutions and difficulties to be overcome are widely diverse. Yet, still remaining in the civil segment, there can be further differences, depending on the size of the aircraft, from large jets, to commuters or general aviation, in turn classifiable in tourism, acrobatic, ultralight and so on, each with their own peculiarities. The paper wants therefore to try to trace a common technology denominator, if possible, and envisage a future perspective of actual applications.
Bio: Antonio Concilio took his degree in Aeronautics Engineering with honour at the University of Napoli "Federico II" (Italia) in 1989; there, he was also awarded his PhD in Aerospace Engineering in 1995.In 2007 he completed the ECATA Master in Aerospace Business Administration, at ISAE-Supaero, Toulouse (France). Since 1989 he works as a Researcher at the Italian Aerospace Research Centre (Italia), where he is currently the Head of the Adaptive Structures Division. Since 2005, he is a lecturer at the PhD School "SCUDO" at the University of Napoli "Federico II" ("Introduction to Smart Structures, Theory and Applications"). He is author of about 200 scientific papers, presented at conferences or published into specialised journals.