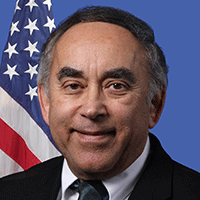
Monday, April 29, 9:15am – 10:15am
MATERIALS KEYNOTE
Dr. Larry Ilcewicz
Chief Scientific and Technical Advisor, Composite Materials
Federal Aviation Administration
Keynote Title Effects of Material & Process Control on Composite Aging
Abstract: This seminar summarizes existing practices for composite aircraft certification, with an emphasis on structural aging aspects, and discusses the limitations and lessons learned from today's "traditional" composite structures. It describes procedures that can be used to certify innovative designs that use advanced materials and processes which may have increased levels of variability, unfamiliar structural performance, nonclassical (e.g., nonlocal) behavior, and unique properties. Provided such complexity can be reliably controlled by design, while maintaining repeatable materials and processes in fabricating and assembling parts, both design and production certification can be achieved. When successful, related technical advances from real applications will meet safety, form, fit and functional requirements, while achieving product value to manufacturers, suppliers, partners and customers. Practical experiences derived from applications using team members with numerous engineering, business, and other skills, provides crucial base knowledge for the future workforce needs of industry. The discussion will cover many engineering aspects, including mechanical, chemical, industrial, and manufacturing, as well as risk management within the safety continuum for numerous aircraft product types.
Biography: Dr. Larry Ilcewicz is the FAA Chief Scientific and Technical Advisor for Composite Materials. He started work with the FAA in 1998 and has supported many certification activities for small airplanes, rotorcraft and transport aircraft. He has also worked on accident investigations and service problems involving composites. These experiences helped Larry develop an international plan for composite safety and certification initiatives to work with industry, academia, and other government groups in pursuit of guidance, training and standardization. These efforts formed the basis for a FAA Aviation Safety Composite Plan, which outlines work until 2027.
Larry came to the FAA from Boeing, where he worked 17 years on various programs in the commercial transport aircraft division, including support to 737, 757, 767 and 777 aircraft in various stages of development, production, and service. Larry was also principal investigator for NASA-funded research to develop composite design and manufacturing concepts for a wide-body transport fuselage in the 1990s. Boeing helped sponsor his PhD in Mechanical Engineering at Oregon State University. Larry has authored/co-authored more than 90 technical publications, including several FAA policy and guidance documents. He has been co-chairman for Composite Materials Handbook 17, CMH-17, since joining the FAA. In 2013, he received the Presidential Rank Award and, in 2018, he received the American Institute of Aeronautics and Astronautics Crichlow Trust Prize.
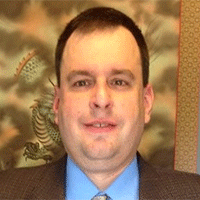
Tuesday, April 30, 9:15am – 10:15am
STRUCTURES KEYNOTE
Dr. Andrew Littlefield
US Army DEVCOM AC Benet Labs
Keynote Title: Application of Composites and Additive Manufacturing to Armament Systems
Abstract: The emphasis on lightweight large caliber weapons systems has placed the focus on the use of advanced composite materials. In the past composites have been applied to direct fire cannons and electromagnetic railguns. Those efforts focused on thermoplastics and high-tension winding. Unfortunately, traditional thermoplastics cannot handle the temperatures needed for howitzer and mortar applications.
For howitzers there are traditional thermosets that can handle the use temperatures, but they cure at high temperatures, and this results in a gap forming between the tube and the gun tube. Service temperatures for a mortar tube exceed the temperature capability of most high temperature thermoset materials during rapid fire, with high bore pressures and propellant flame temperatures exacerbating the problem. The mortar baseplate couples the load directly to the ground from any firing angle and any soil resulting in a very complex loading situation. Several efforts are currently underway to deal with these applications.
Armaments, especially large caliber armaments, tend to be complicated, highly loaded, and low production rate items. The complicated geometries and low rates of production lends itself to additive manufacturing (AM). One extremely attractive benefit of AM is the ability to print at the point of need. This ability can greatly simplify the logistics train and will help units stay in the fight even when cut off from resupply. However, until recently the high material property requirements and physical size have made converting these parts to AM impractical.
One current AM effort is a 155mm muzzle brake. This brake is currently cast with long lead times and a significant portion require rework. The part is roughly 33 inches long, 15 inches tall and 20 inches wide. Attempts have been made to manufacture this brake via Electron Beam Additive Manufacturing and Wire Arc Additive Manufacturing. Additionally, an effort is underway to optimize the design and print it using laser powder bed fusion.
Another effort is focused on evaluating bound metal printing as possible means of fabricating at the point of need. A program is underway to compare bound metal solutions from MarkForged, BASF, Rapida and others. The program will consist of printing coupons and conducting material property testing to compare these different materials / systems. Parts will then be fabricated, and field tested.
This presentation will go over these and other efforts currently underway at the DEVCOM Armaments Center along with their goals, progress, and future plans.
Biography: Dr. Littlefield is the lead composite engineer at CCDC AC Benét Laboratories, Watervliet, NY, where he works on composite gun tubes and shrouds, electromagnetic railgun launchers, gun barrel vibration absorbers, and simulated proof testing of mortar base plates. Prior to joining CCDC AC, he worked for the U.S. Air Force Research Laboratory on applying composites to spacecraft structures. He received the 2010 Army Science Conference Best Paper Lethality Award and several research and development awards. He has authored several journal and conference papers and technical reports. He has patents for a self-powering prognostic gun tag, an electromagnetic gun launcher, and composite mortar base plate and tube. Dr. Littlefield holds a Ph.D. in mechanical engineering from Rensselaer Polytechnic Institute (RPI).
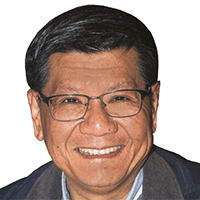
Wednesday, May 1, 9:15am – 10:15am
STRUCTURAL DYNAMICS KEYNOTE
Dr. Nhan Nguyen
Technical Group Lead
Advanced Control and Evolvable Systems Group
Intelligent Systems Division
NASA Ames Research Center
Keynote Title: Adaptive Aeroelastic Wing – Enabling Sustainable Aviation
Abstract: Adaptive wing is viewed as a key enabling technology in modern aircraft design to achieve sustainable aviation. In this talk, research on NASA performance adaptive aeroelastic wing technologies will be presented. Shape-changing concepts and active aero-structural control technologies will provide integrated strategies to enable future adaptive wing aircraft design. Experimental validation efforts are conducted by NASA jointly with industry and academia to mature adaptive wing technologies.
Biography: Dr. Nhan Nguyen is a senior technical group leader of the Advanced Control and Engineering Systems (ACES) research group at NASA Ames Research Center. He is managing a 22-person research group conducting research & development in advanced flight control and structural control of aerospace vehicles. He previously held leadership positions with NASA Aeronautics Research Mission Directorate as project scientist and deputy project manager of the Integrated Resilient Aircraft Control project in charge of developing research implementation at four NASA aeronautics centers. Dr. Nguyen has published more than 290 technical publications and one textbook. His research impact covers the convergence of control theories, flight vehicle dynamics, and structural dynamics. He developed advanced adaptive flight control flown onboard F-18 aircraft and mission-adaptive wing shaping control for high-aspect ratio wing aircraft. He was awarded NASA’s prestigious Exceptional Scientific Achievement Medal for significant scientific contributions in the advancement of these new capabilities. He is also the recipient of more than 60 other NASA honors and awards. He is the holder of 8 U.S. patents. Dr. Nguyen is an adjunct professor at University of California Santa Cruz. He is an associate fellow of the American Institute of Aeronautics and Astronautics and a former chair of the Intelligent Systems Technical Committee.