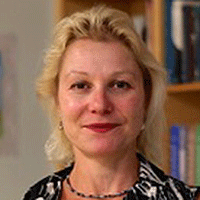
Tuesday, November 1, 9:15AM - 10:00AM
Name: Julia Greer
Presentation Title: Materials by Design: Three-Dimensional (3D) Nano-Architected Meta-Materials
Abstract: Creation of extremely strong and simultaneously ultra lightweight materials can be achieved by incorporating architecture into material design. Dominant properties of such meta-materials are driven by their multi-scale nature: from characteristic microstructure (atoms) to individual constituents (nanometers) to structural components (microns) to overall architectures (millimeters+). To harness the beneficial properties of 3D nano-architected meta-materials, it is critical to assess their properties at each relevant scale while capturing overall structural complexity.
Our research is focused on design, synthesis, and characterization of nano-architected materials using nanofabrication and additive manufacturing (AM) techniques, as well as on investigating their stimulus-driven response as a function of architecture, constituent materials, and microstructure. These "meta-materials" exhibit superior and often tunable properties, i.e. resilience against impact, recoverability, failure suppression, anisotropic stiffness; nano-photonic response (PhCs); new electrochemical degrees of freedom (Li-ion batteries), and shape memory response (SMPs) at extremely low mass densities, as well as lend themselves to novel functionalities (hydrogel-enabled synthesis) which renders them useful and enabling in technological applications. We strive to uncover the synergy between atomic-level microstructure and nano-sized external dimensionality, where competing material- and structure-induced size effects drive overall response. My talk with focus on additive manufacturing via function-containing chemical synthesis to create nano- and micro-architected metals, ceramics, multifunctional metal oxides, and shape memory polymers, as well as demonstrate their potential in some real-use applications. I will describe how the choice of architecture, material, and external stimulus can elicit stimulus-responsive, reconfigurable, and multifunctional response.
Bio: Greer's research focuses on creating and characterizing classes of materials with multi-scale microstructural hierarchy, which combine three-dimensional (3D) architectures with nanoscale-induced material properties. We develop fabrication and syntheses of micro- and nano-architected materials using 3D lithography, nanofabrication, and additive manufacturing (AM) techniques, and investigate – among others - their mechanical, biochemical, electrochemical, electromechanical, and thermal properties as a function of architecture, constituent materials, and microstructural detail. We strive to uncover the synergy between the internal atomic-level microstructure and the nano-sized external dimensionality, where competing material- and structure-induced size effects drive overall response and govern these properties.
Greer obtained her S.B. in Chemical Engineering from MIT in 1997 and a Ph.D. in Materials Science from Stanford. She currently is a Ruben F. and Donna Mettler Professor of Materials Science, Mechanics, and Medical Engineering at Caltech. Greer is also the Director of the Kavli Nanoscience Institute at Caltech.
Greer has more than 150 publications, has an h-index of 65, and has delivered over 100 invited lectures, which include 2 TEDx talks, the Gilbreth Lecture at the NAE, the Midwest Mechanics Lecture series, and a “IdeasLab” at the World Economic Forum, and was recently selected as Alexander M. Cruickshank (AMC) Lecturer at the Gordon Research Conferences (2020). She received the inaugural AAAFM-Heeger Award (2019) and was named a Vannevar-Bush Faculty Fellow by the US Department of Defense (2016) and CNN’s 20/20 Visionary (2016). Her work was recognized among Top-10 Breakthrough Technologies by MIT’s Technology Review (2015).
Wednesday, November 2, 9:45AM - 10:30AM
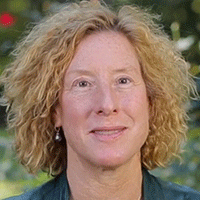
Name: L. Cate Brinson
Title: Materials Data & Informatics: Curation, Frameworks, Access, and Potential for Discovery and Design
Abstract: With the advent of the materials genome initiative (MGI) in the United States and a similar focus on materials data around the world, numerous materials data resources and associated vocabularies, tools, and repositories have been developed. While the majority of these systems focus on slices of computational data with an emphasis on crystallographic materials, platforms for organic materials and their composites, especially those incorporating experimental data, have been quite limited. We will discuss the unique aspects of tackling data assembly and informatics associated with experimental organic materials data, with focus on our experiences creating an open-source data resource, NanoMine, part of MaterialsMine. Our goal has been to curate, annotate and store widely varying experimental data on polymer nanocomposites (polymers doped with nanofiller) and providing access to characterization and analysis tools with the long-term objective of promoting facile nanocomposite design. The challenges and promises associated with data curation, ontology and vocabulary development, standardization and interoperability, and data visualization and analysis tools will be discussed. Several case studies will be presented, including use of natural language processing for archival data curation, coupling of experimental and computational data for materials design, and development of machine learning tools for rapid property screening and inference. Overall, we focus on the promise of this new approach to tackle materials design principles for the complex, high dimensional problems inherent in the multi-phase polymer space.
Bio: L. Cate Brinson is the Sharon C and Harold L Yoh III Professor of Engineering and the Donald M Alstadt Department Chair of the Mechanical Engineering and Materials Science Department at Duke University. Following her PhD from Caltech and a postdoc in Germany, she was a faculty member at Northwestern University until her move in 2017 to Duke University. Current research involves characterization of local polymer mechanical behavior (including composites and 3d printed constructs) and materials genome (data) research, where investigations span the range of molecular interactions, micromechanics and macroscale behavior. Dr. Brinson has received a number of awards, including the the Eringen Medal of SES, the Nadai Medal of the ASME, the Friedrich Wilhelm Bessel Prize of the Alexander von Humboldt Foundation, the ASME Tom JR Hughes Young Investigator Award, and an NSF CAREER Award, and she is a Fellow of many professional societies. She has authored one book and over 170 refereed journal publications with over 25000 citations and an h-index of 70. Her book has had over 60,000 chapter downloads from the e-version since publication in 2008 and a second edition published in 2015. She served 5 years on the Society of Engineering Science Board of Directors, including one year as President, and is a founding member of the Materials Research Data Alliance (MaRDA).