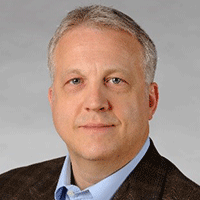
Organizer: Benjamin Leever
Moderator: Benjamin Leever
Keynote Speaker: John Yundt, SunRay Scientific
Abstract: Advancements in the development of Flexible Hybrid Electronics (FHE) materials and technologies continue to progress rapidly; nonetheless, high-volume manufacturing of complex FHE-based products with high reliability remains elusive. This issue becomes even more noteworthy especially in regards o printable wearable applications and technologies. Beyond flexible electronic devices that are inherently bendable, stretchable electronic devices are the next evolutionary developmental need for a wide array of real-world applications. Due to the nature of the biaxial strain induced during use, such stretchable devices are expected to be mechanically robust while maintaining electrical performance even under dynamic high tensile strains. Most of these stretchable electronic devices are hybrid in nature; being comprised of both soft and rigid electronic components. Hence, robust and reliable electrical interconnections between such soft and rigid components are necessary to ensure proper functionality of the device. Currently, interconnections between functional electrical systems and the wearable e-textile materials utilize traditional methods such as high-pressure Anisotropic Conductive Adhesives or Films (ACA/ACF), rigid solder connections, snap/cinch connections, and isotropic conductive adhesives (ICA). Each of these interconnection methods pose a variety of issues with the necessary material sets for wearables/e-textile materials. There are significant drawbacks related to mechanical and/or thermal damage during the connection process; poor mechanical adhesion; inability to connect standard-pitch functional devices; and lack of robustness when connecting to nonplanar surfaces seen in wearable device configurations. Additional challenges with these interconnect methods limit high-volume manufacturing of such products. SunRay Scientific Inc. will present recent results in the development of a novel anisotropic conductive adhesive, ZTACH® ACE, for high-volume surface mount assembly of electrical components, including those elements mounted/attached to flexible, stretchable membranes and textiles in wearable applications.
Prior research and development have demonstrated the technology behind ZTACH® ACE with superior performance in achieving environmentally stable and mechanically robust electrical connections. For improved manufacturability, this interconnect method allows for pressure-less assembly, low-temperature cure, excellent adhesion to a variety of substrates, and fine pitch reliability without sacrificing contact resistance or mechanical bond integrity. The ability of ZTACH® ACE to concurrently serve as its own underfill and edge encapsulant improves reliability especially with respect to the rigors of use in typical wearable applications on host substrates like textiles and TPU. It has been shown that ZTACH® ACE interconnects do not experience the same types of failures conventional competing technologies experience without the addition of underfill and/or encapsulation. In providing superior adhesion, low contact resistance, and mechanical robustness during electromechanical testing, ZTACH® ACE proves itself to be a reliable interconnect solution between stretchable to stretchable/flex/rigid materials with high electrical conductivity. With demonstrated scalability, these attributes enable easier and lower cost manufacturing of more flexible and robust applications through integration of SMD components directly onto e-textiles, without needing additional laminated protective layers. As a result, flexible wearable printed electronics can readily be incorporated into a wider range of cost-effective, reliable end use applications.
Beyond Flexible – Stretchable Electronic applications, ZTACH® ACE is suitable for semiconductor interconnect needs given high-yield finer pitch attributes. Successful developments have been achieved with demonstrations of IR FPAs, large-format area arrays, and RF applications. Continuing materials and processing maturation of this technology is expected to substantially address reliability and longevity requirements along with appreciable low-cost advantages most needed for semiconductor packaging and assembly.
Biography: John M. Yundt Vice President of Sales & Business Development, SunRay Scientific, Inc.
John is a graduate of Western Illinois University, with 28 years of experience in printed electronic materials and conductive coatings. Beginning his career at Acheson Industries (now part of Henkel), John became Business Development Manager, North America before leaving to start the Printed Electronics business at Spraylat Corporation. For the past decade John was Global Business Manager for PPG’s Electronic Materials business prior to joining SunRay Scientific in July of 2021.