Monday, July 24
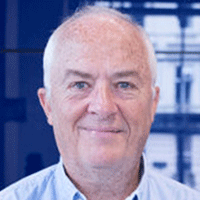
Professor Michael Lowe, Ph.D.
Faculty of Engineering, Department of Mechanical Engineering
Head of Department of Mechanical Engineering
Imperial College London
Lecture Title: Numerical simulation of ultrasound for research in NDE
Abstract: The capabilities of performing ultrasound NDE have progressed enormously in recent years. A key driver to enable this progress has been the advent of effective accurate computational tools for the simulation of ultrasound waves and their behaviour. These tools were rare and specialist even just 30 years ago but are commonplace on desktop computers affordable by all researchers today.
Simulation models enable the investigation of ultrasound behaviour in general, such as the nature of wave propagation and scattering, but they also allow for specific simulations of trial setups, postulated defects and material properties, which inform the capabilities when planning inspections.
Simulations of this kind are now so realistic that they are being used in the role of experiments, to demonstrate with precision what happens with particular choices of setup equipment and parameters, and to determine the sensitivity of these setups to the detection and characterising of defects. They are also used to evaluate the quality of theoretical models when these models necessarily include approximations, to identify the significance of the approximations. Yet further along this path, they can now replace laboratory measurements when there is definable uncertainty, such as lack of knowledge of specific details of defects or materials, by being able to deliver statistical results that are unattainable experimentally. The current challenge being pursued beyond that is the realistic incorporation of unknown elements of measurement, such as transducer contact conditions and measurement noise.
The presentation will chart the recent history in the development of Finite Element simulations for the development of ultrasound NDE, including examples of uses from academic research challenges to industrial applications. Critically, it will show how the accepted use of these models is changing, with increasing confidence, from being a demonstrator of behaviour to approaching the ground truth, or the “gold standard” solution. This is an emerging role as an ideal form of experimentation, finding its place in research for NDE.
Biography: Michael Lowe received a BSc degree from the University of Edinburgh in 1979, and an MSc and PhD in Mechanical Engineering from Imperial College in 1987 and 1993 respectively. Between 1979 and 1989 he worked for WS Atkins (Consultant Engineers, Epsom, UK), specialising in the application and development of numerical methods for the solution of problems in solid mechanics. In 1989 he moved to a research position at Imperial College London, was appointed as an SERC Research Fellow in 1992, and onto the academic staff in 1994.
His research is in Non Destructive Testing (NDT), with particular interests in structure-guided ultrasound, wave theory, wave scattering, materials characterisation, and analytical and numerical modelling. His teaching interests are in mechanics, stress analysis, mathematics, vibration, and Finite Element modelling.
He is currently Head of the Department of Mechanical Engineering.
He was elected Fellow of the Royal Academy of Engineering in 2014. He is a director of Guided Ultrasonics Ltd, a spin-out company which was set up to commercialise the outputs of research in ultrasonic guided waves. He was the creator of the leading software modelling tool DISPERSE (www.disperse.software) which calculates the properties of elastic/sound waves that are guided in structural forms such as plates and pipes. He was a co-founder of the UK Research Centre in Non Destructive Evaulation (RCNDE) which has run since 2003; this is a joint industry-university organisation for coordinating and delivering research in NDE.
Tuesday, July 25
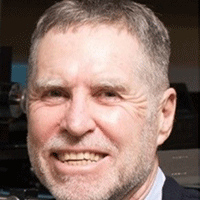
Victor Giurgiutiu, PhD, PE, FRAeS, F.ASME, AF.AIAA
John Ducate Sr. Chaired Professor of Mechanical Engineering
Director, Laboratory for Active Materials and Smart Structures
University of South Carolina
Lecture Title: SHM of Advanced Composites – Challenges and Opportunities
Abstract: The development of adequate NDE and SHM techniques for composite structures is much more challenging than for metallic airframes. While the damage and failure of metallic structures is relatively well understood, the damage in composite materials is much more complicated and less understood. For metallic structures, in-service damage and failure occur mostly due to fatigue cracks that propagate under cyclic loading and may be accelerated by corrosion and other environmental factors. For composite structures, the situation is more complex: composites fail differently under tension than under compression and the effect of fastener holes is much more complicated than in metals. In addition, the composites are prone to hidden damage from low velocity impact (e.g., the drop of a hand tool on a wing, or large hail impact on a radome); such barely visible damage (BVD) may go undetected, but its effect on the degradation of the composite structure strength can be dramatic.
This presentation starts by reviewing the basic properties of anisotropic composite and their major damage types, both due to fatigue and degradation under normal operation condition and due to accidental BVD events. Next, the presentation will review the major sensor types and damage sensing techniques employed so far for composite SHM such as piezo transducers, fiber optics, strain gages, composite electrical properties, etc. Examples from the available literature will be critically discussed.
The presentation will next focus on predictive modeling of composite response to various SHM interrogation techniques. Stress, vibration, and wave analysis methods will be briefly reviewed. Emphasis will be given to modeling of guided wave propagation in composite with the emphasis on predicting the sensor response to various damage situations. Comparison with carefully conducted experiments will be provided. The presentation will end with a summary of the major challenges for composites SHM and identify some opportunities for going forward.
Biography: Dr. Victor Giurgiutiu has a wide research interest in structural mechanics that spans active materials, smart structures, structural health monitoring, mechatronics, and other multi-physics applications. Dr. Giurgiutiu has published widely. He is widely cited worldwide. His book Structural Health Monitoring with Piezoelectric Wafer Active Sensors (Elsevier Academic Press, 2008) has been cited ~2,000 times, and two of his papers have received 1148 and 764 citations, respectively.
Dr. Victor Giurgiutiu is Fellow of the Royal Aeronautical Society (RAeS), Fellow of ASME and Associate Fellow of AIAA. He serves as Special Issues Editor to the Structural Health Monitoring – An International Journal (Sage, UK) and Associate Editor to the Aeronautical Journal of RAeS. He was recognized as Structural Health Monitoring Person of the Year 2003. During 2006-2009 he served as Structural Mechanics Program Manager with the Air Force Office of Scientific Research (AFOSR). Dr. Giurgiutiu received a BSc(Eng) in Aeronautics (1972) and a PhD in Aeronautical Structures (1977) from Imperial College, London, UK.
Wednesday, July 26
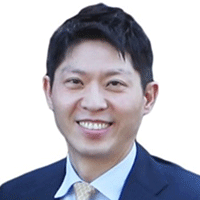
Hoon Sohn, Ph.D.
Professor
Korea Advanced Institute of Science and Technology (KAIST)
Lecture Title: Online Nondestructive Testing and Quality Control During Metal Additive Manufacturing
Abstract: Additive manufacturing (AM), also known as 3D printing, is revolutionizing how various structural components are manufactured. Laser Powder Directed energy deposition (LP-DED), which is one time of metal AM processes, utilizes a concentrated laser source and metal powders to achieve layer-by-layer deposition of materials. Although significant progresses have been made for the development of DED processes and materials, little work has been done for online nondestructive testing and quality control. In this study, a suit of online nondestructive testing (NDT) and process control techniques are developed, including (1) melt pool depth estimation using coaxial infrared camera, (2) porosity inspection based on transient thermoreflectance measurement using femtosecond laser, (3) mechanical properties estimation based on noncontact ultrafast ultrasonic measurement, (4) porosity reduction and microstructure improvement using a Nd:YAG pulse laser, and (5) track-wise geometry monitoring using laser line scanner.
Biography: Hoon Sohn received his B.S. and M.S. degrees from Seoul National University, Seoul Korea and Ph.D. from Stanford University all in Civil Engineering. He worked at Los Alamos National Laboratory (LANL) as a Technical Staff Member and at Carnegie Mellon University as an Assistant Professor. He is now a Professor at KAIST (Korea Advanced Institute of Science and Technology) in South Korea. His research interest has been in the areas of structural health monitoring, nondestructive testing, sensing technologies and data analytics. He has published over 210 refereed journal articles, over 400 conference proceedings, and 12 book & book chapters. He is holding 28 domestic and 14 international patents, and his developed technologies are licensed and commercialized by private companies, resulting in over 1 Million USD licensing agreements. He is currently SPIE Fellow, Member of National Academy of Engineering of Korea (NAEK), and Member of Korean Academy of Science and Technology (KAST).
Thursday, July 27
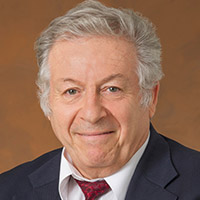
Yoseph Bar-Cohen, Ph.D.
Senior Research Scientist
Jet Propulsion Lab (JPL)
Lecture Title: Humanlike Robots as Artificial Inspectors: The Science Fiction and Engineering Reality
Abstract: Human errors have long been recognized as a major factor in the reliability of nondestructive evaluation results. To minimize such errors, there is reliance on automatic inspection tools that allow faster and consistent tests. For rapidly inspecting complex structures in the field, crawlers and various manipulation devices are commonly used to perform variety of inspection procedures that include C-scan with contour following capability. The industrial use of robots has been the result of the need to deal with parts that are too complex to handle by a simple automatic system. For decades already, automation tools were used to inspect full structures at the quality assurance of manufacturing and maintenance facilities. Human-like autonomous robots can potentially address the need to inspect structures with configuration that are not predetermined. The operation of such robots may take place at harsh and hazardous environments that are too dangerous for human presence. Biomimetic technologies such as artificial intelligence, artificial muscles, artificial vision, and numerous others are increasingly becoming common engineering tools in making robots. Inspired by science fiction, humanlike robots are increasingly becoming an engineering reality, and in the future, they may potentially replace human inspectors. In this presentation, the state-of-the-art of humanlike robots will be reviewed and the outlook for their future operation as inspectors will be discussed.
Biography: Dr. Yoseph Bar-Cohen is a Senior Research Scientist and a Group Supervisor at Jet Propulsion Lab (JPL). He received his Ph.D. in Physics from the Hebrew University, Jerusalem, Israel, in 1979. His research is focused on electroactive mechanisms, biomimetics and NDE. He has edited and coauthored 12 books, co-authored over 460 publications, and co-chaired 56 international conferences. He covered his co-conceived inventions in 42 registered patents and 135 New Technology Reports (NTR). His notable initiatives include the SPIE conference on electroactive polymers (EAP) and the EAP-in-Action Session that he chaired for 22 years as well as his challenging engineers and scientists worldwide to develop a robotic arm driven by artificial muscles to wrestle with human and win. For his contributions to the field of artificial muscles, Business Week named him in April 2003 one of five technology gurus who are "Pushing Tech's Boundaries". His scientific and engineering accomplishments earned him two NASA Honor Award Medals, two SPIE’s Lifetime Achievement Awards, Fellow of two technical societies: ASNT and SPIE, as well as many other honors and awards.