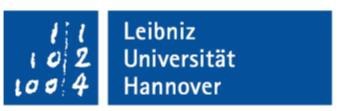
The AMRGT seminars will be held on Tuesday, March 3, 2020.
MRO Concepts for the Future: New Approaches of Business, Engineering, Repair and Logistics
Speakers
Prof. Dr.- Ing. Joerg Seume, Professor and Head of the Institute of Turbomachinery and Fluid Dynamics, Leibniz University Hannover
Dr. Friedhelm Kappei, MTU Maintenance Hannover GmbH, Germany
The regeneration (also called overhaul) of Complex Capital Goods, such as heavy-duty gas turbines or aircraft engines is of high interest for the operators as it causes a significant part approximately 8% of the operating costs. Approximately 50% of the overhaul costs is caused by the airfoils and therein mainly by the replacement of worn blades from the high-pressure turbine module.
In order to address this business potential, MTU aero Engines, its subsidiary MTU Maintenance, and Leibniz University Hannover (LUH) have developed new conceptual approaches to engineering, production engineering, and logistics in aircraft engine MRO. A joint Center of Competence (CoC) for MRO was established by the MTU and LUH in 2008 and results from the Collaborative Research Centre 871 (CRC 871) “Regeneration of Complex Capital Goods” sponsored by the German Research Foundation (DFG) are used. The main goal is to reuse as many of the worn components as possible. However, the functional properties of jet engines have to be restored and/or even improved. For this purpose, new repair methods are developed and the existing methods are continuously improved to increase flexibility. New manufacturing and logistic processes are developed and model-based simulations assess the functional benefit of regenerated components and of the entire regenerated jet engine. An additional objective is to improve measurement technology to allow an early detection of damage. In particular, methods to analyze the hot-gas path components by performing the optical background-oriented schlieren method or non- destructive characterization of coating and material properties and multi-scale measurement of blade geometries.
The seminar will offer insight into the scientific results and their transfer to future Aero Engine MRO technologies. Some of the featured results will also address the challenges and solutions of modern MRO business models like market trends in air transport, development trends of the legacy fleet and the state-of-the art fleet, and the additionally challenges and approaches for MRO independent of OEMs and airlines. Then an overview will be given of the transfer of the scientific results of the cooperation between the MTU and the Leibniz University to meet the described challenges, including examples from the diagnosis and repair of hot gas path parts and compressor defects. New approaches of the MRO process newly developed solutions in the field of capacity planning, logistics, and process organization will be presented.

Fabrication and Repair of Industrial Gas Turbine Engine Components using Hybrid (Additive/Subtractive) Manufacturing Processes
Speakers
Thomas Feldhausen, R&D Staff Member, Oak Ridge National Laboratory
Michael Kirka, Materials Scientist, Oak Ridge National Laboratory
Vincent Paquit, Senior Research Scientist, Oak Ridge National Laboratory
Moderator
Thomas Kurfess, Chief Manufacturing Officer, Oak Ridge National Laboratory
Hybrid manufacturing is the combination of additive manufacturing (AM) (Deposition) and subtractive manufacturing (machining) inside of the same machine tool. This combination mitigates issues associated with the traditional disjointed processes. A successful repair process that leverages hybrid manufacturing has the potential to result in a 36% energy savings and a 60% reduction of the carbon footprint. This seminar will provide an overview of the current state of hybrid manufacturing technology along with Oak Ridge National Laboratory’s current capabilities in the field. A collaboration between Oak Ridge National Laboratory, Delta Tech Ops, and Georgia Institute of Technology on the additive repair of high-pressure turbine blades will also be discussed. Following an overview of hybrid processes utilized for repair operations, specifics will be presented and discussed related to material properties generated during AM/hybrid operations as well as the data analytics employed to qualify components and control production processes.
Among the challenges facing the wider implementation of Industrial gas turbine engine (IGTE) components fabricated or repaired using AM is the understanding of the process-structure-property relationships which accompany AM materials particularly considering the repair and fabrication and repair of gas turbine components. There is often the desire to apply mechanical property requirements on AM materials which are arbitrarily adopted from materials processed by traditional techniques. Ultimately, these traditional materials vary greatly in microstructure, residual stresses, and thermal histories compared to those fabricated through AM processes. To understand the process-structure-properties of AM fabricated metals, a holistic view is necessary that captures the additional linkage and complexity of geometry in the AM process and the manner through which geometry impacts process-structure-properties. Using such an approach, the process can be tailored within reason to achieve the target repeatable end-result properties.
While the properties of IGTE relevant AM materials can be shown to meet application needs, certifying and qualifying the materials and/or parts from the AM process is a challenge due to the complex and unknown nature of the AM processes along with interpreting the unprecedented amounts of process data streams (in-situ process monitoring, machine process data, ex-situ data). Data analytics presents an opportunity for processing and co-registering of available data streams from the AM processes. To be discussed is a case study for the certification and qualification of a prototype airfoil set fabricated through AM while leveraging data analytics techniques to enable inspection and comparison of each airfoil on a voxel by voxel basis to capture defects and build quality concerns.
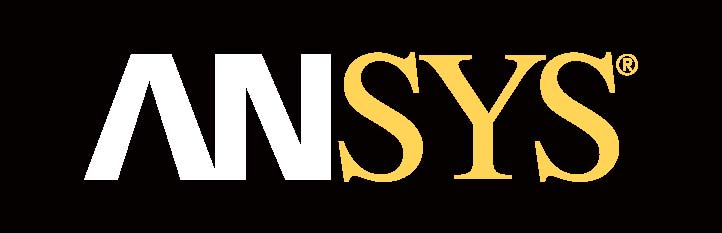
Additively Manufactured Product Development Cycle Improvements through Simulation
Speakers
Chris Robinson, Software Development Manager, ANSYS, Inc.
Tim Gornet, Manager: AMIST Core Facility, University of Louisville Additive Manufacturing Institute of Science and Technology (AMIST)
The gas turbine industry can benefit greatly from potential added value provided through additive manufacturing (AM) complex and efficient products. However, the current product development cycle has limitations that slow the progress of AM product development. While some of the barriers to a better cycle are related to the manufacturing process itself, many are related with understanding the process. Gaining better understanding of the manufacturing process and effectively controlling that knowledge through data management greatly improves the Development Cycle for Additive Manufacturing.
There are software tools to help in every step of the AM product development cycle from design to qualification. Design optimization tools aid users in rapidly designing a product from a performance and manufacturing perspective. Structural, thermal, fluid and other simulation techniques provide validation of an optimized design. Designers, analysts, material scientists, process engineers, and manufacturers all need to understand the impact of the Additive Manufacturing process on the designed component in order to produce the optimal geometry. Software can support determining the optimal orientation for fabrication, the appropriate fixturing of the part during the build process (supports), processing parameters, and issues that are likely to arise during the manufacturing process. Process simulation can give insight into distortion, stress accumulation, porosity, and microstructural grain orientation and size under given manufacturing conditions to assist in correcting problems before they ever occur. Data management without a sophisticated tool can become so cumbersome that it can bring the product development cycle to a halt, but tools are available that manage traceability from raw materials and manufacturing equipment to process conditions and on through to inspection and testing data.
This seminar will present the suite of ANSYS tools that address the AM product development cycle with examples of how the tools can be used to improve the process. Attendees will gain insight into how some of these tools are used daily at AMIST. Case study examples of how these tools have been used to address complex AM specific problems will also be shared and discussed.