Plenaries are general sessions that will be opening each day of the conference for the Fluids Engineering Division Summer Meeting.
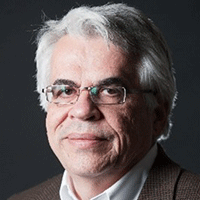
Monday, July 28, 2025 | 8am – 9am (local time)
Michael Triantafyllou
Henry L. and Grace Doherty Professor of Ocean Science and Engineering
Department of Mechanical Engineering
Massachusetts Institute of Technology
Presentation Title: From Biomimetic Fluid Mechanics to "Intelligent" Hydrodynamics
Abstract: Unsteady flow-structure interaction problems, such as fish-like swimming, have fascinating properties but involve complex physical mechanisms presenting formidable difficulties to explore them experimentally and computationally. We show how two powerful methodologies, Biomimetics, the science of exploring the function of animals in order to emulate their performance, and Artificial Intelligence (AI) methods, have proven to be powerful tools for elucidating the basic mechanisms involved and implementing novel flow control methods.
We first show how the biomimetic study of fish-like swimming has unveiled the mechanisms for flow control that animals have perfected through evolution, leading to the development of scaling laws for vorticity control in propulsion and maneuvering, methods to control turbulence in unsteady flows, and ways to achieve super-maneuverability.
Next, we show how using AI methods, strategies were developed to expedite by orders of magnitude experimental mapping of the properties of flow-structure interaction problems that depend on multiple parameters, offering unprecedented new capabilities to identify the parametric effect on the dominant physical mechanisms in order to optimize system configurations. We show two example cases, first, the development of the "Intelligent Towing Tank" that used Gaussian Process Regression to map the properties in combined in-line and cross-flow vortex induced vibrations of flexibly mounted cylinders as function of the Reynolds number. Then the same tank was used to maximize the wave energy dissipation of architected artificial reefs with controlled porosity, providing drag coefficients at least an order of magnitude larger than existing reefs.
Biography: Michael Triantafyllou is the Henry L. and Grace Doherty Professor in Ocean Science & Engineering in the Department of Mechanical Engineering at the Massachusetts Institute of Technology. He is the Director of the MIT Sea Grant Program.
He teaches and has published over 370 journal articles and refereed conference papers in the areas of biomimetic robotics and sensing, dynamics and control of marine systems, cable mechanics, and experimental fluid mechanics. He pioneered the development of science-driven biomimetic robots to study the basic mechanisms of flow control that lead to the outstanding agility of fish and cetaceans. The RoboTuna original design is at the Science Museum in London, while a second version of the robot shown at left, is on exhibit at the MIT Museum. He is currently applying machine learning methods for flow control to increase hydrodynamic performance and maneuvering of marine vehicles, and he is developing digital twins for the offshore industry.
He is a Life Fellow of the American Physical Society and a Life Fellow of the Society of Naval Architects and Marine Engineers.
He served as Associate Department Head in the Department of Mechanical Engineering (2008-2010), Director of the Center for Ocean Engineering (2005-2017) and is a Visiting Scientist at the Woods Hole Oceanographic Institution since 1991. He is serving on the American Bureau of Shipping's Marine Technical Committee since 2015. He was Chairman of the Board of the National Technical University of Athens (2013-2017).
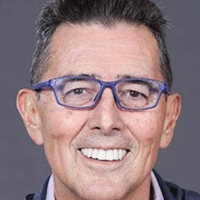
Tuesday, July 29, 2025 | 8am – 9am (local time)
Luis San Andrés
Professor Emeritus
Texas A&M University
Presentation Title: Wet Annular Seals in Multiphase Pumps: Leakage and Rotordynamic Force Coefficients and a Method to Promote Seal Direct Stiffness
Abstract: In the subsea oil and gas industry, multiphase pumps enable a long-distance tie back system and eliminate topside oil and gas separation stations. A persistent challenge to operate (vertical) centrifugal pumps handling (gas in liquid) mixtures is their poor reliability due to persistent sub synchronous vibrations (SSV). The gas volume fraction (GVF), changing over the life of the well, affects the dynamic forced performance of annular clearance seals, and which may lead to an increase in both lateral and axial rotor vibrations. The lecture presents measurements of leakage and dynamic force coefficients for a grooved seal and a wavy-clearance seal. The seals, short in axial length (L=0.342D), are typical as interstage bushing or impeller front wear ring seals. A mixture of air in ISO VG 10 oil with inlet gas volume fraction (GVF) ranging from 0 (just oil) to 0.8 (mostly air) lubricates the seals. The operating shaft speed equals 3.5 krpm (surface speed = 76.4 ft/s (23.3 m/s)) and the pressure ratio (inlet/exit) = 2.5 for the wavy seal and 2.9 for the grooved seal. Dynamic loads exerted on the seal housing with a single frequency (max. 140 Hz) serve to identify the frequency dependent rotordynamic force coefficients for each seal. Large vertical turbines/pumps have very low natural frequencies and often show subsynchronous vibrations. Local injection of air into the seals alleviates the issue as it reduces the amplitude of rotor motions. The lecture shows the outcome of measurements with local gas injection (GVF~0→10%) to demonstrate a uniform clearance annular seal recovers a positive dynamic stiffness, hence promoting rotor stability. The results validate a well-known practice used to stabilize large vertical pump systems.
Biography: Luis San Andrés, former Mast-Childs Chair Professor of Mechanical Engineering at Texas A&M University (1991-2023), conducted experimental and analytical research on the rotordynamics of pump seals for rocket engine turbopumps and electrical submersible pumps and compressor seals for oil and gas applications. Luis is a Life Fellow of ASME, STLE, GPPS, and a member of the Industrial Advisory Committees for the Texas A&M Turbomachinery and Pump Symposia. Dr. San Andrés and graduate students published over 200 journal papers, several recognized as best in various international conferences.
ASME distinguished Dr. San Andrés with the 2022 Aircraft Engine Technology Award (International Gas Turbine Institute), the 2023 Mayo D. Hersey Award (Tribology Division), and the 2025 Henry R. Worthington Medal for his contributions to pump rotordynamics.
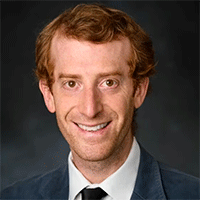
Wednesday, July 30, 2025 | 8am – 9am (local time)
Jason Rabinovitch
Assistant Professor
Department of Mechanical Engineering
Stevens Institute of Technology
Presentation Title: High-speed Compressible Flows and Space Exploration!
Abstract: High-speed compressible flows are relevant to a variety of different space applications. This talk will highlight ongoing research efforts related to three specific topics encompassing both engineering and planetary science applications: 1) modeling supersonic parachute inflations for Mars spacecraft, 2) investigating the eruption mechanism of the Enceladus plume, and 3) describing an exciting new mission concept, VATMOS-SR, that could return a sample of Venus' atmosphere to Earth in less than a year! The first topic addresses the challenges of modeling a single-point failure system for a multi-billion-dollar spacecraft during the Entry, Descent, and Landing (EDL) phase of a mission, and the second topic focuses on a geophysical flow (the jets erupting from the south pole of Enceladus, a moon of Saturn), that potentially shares some similarities with terrestrial volcanism. The VATMOS-SR mission concept highlights the potential complexities of sampling atmospheric gases in a rarefied environment while a spacecraft is traveling > 10 km/s.
Biography: Jason Rabinovitch is an Assistant Professor in the Mechanical Engineering Department at Stevens Institute of Technology (Hoboken, NJ, USA). Before Stevens, Jason was a Mechanical Engineer at NASA’s Jet Propulsion Laboratory (JPL), California Institute of Technology, where he worked in the Entry, Descent, and Landing & Formulation Group for ~6.5 years. He received a B.Sc. in Mechanical Engineering from Yale University in 2008, a M.Sc. in Aerospace Engineering from the California Institute of Technology in 2009, a M.Sc. in Fluid Mechanics from École Polytechnique (Paris) in 2010, and a Ph.D. in Aeronautics from Caltech in 2014. While at JPL, Jason was fortunate to work on a wide range of projects, from delivering flight hardware to the Mars 2020 mission, designing, implementing, and testing a low-density low-speed open jet fan-array wind tunnel for the (successful!) Mars Helicopter, to developing a hybrid rocket propulsion system for small satellites. His current research interests span a wide range of topics related to experimental and computational fluid mechanics applied to EDL, vehicle design, propulsion, and geophysical applications.