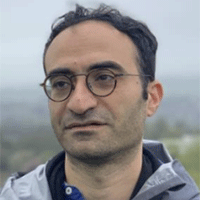
Symposium 1 Invited Speaker
Dr. Sameh Tawfick
Associate Professor of Mechanical Science and Engineering
The University of Illinois Urbana-Champaign
Presentation Title: Design Principles for the Use of Artificial Muscles in Soft and Miniature Robotics
Abstract: In this talk I will describe the design motif known as "antagonistic pairs", commonly observed in skeletal muscles. This arrangement enables the reversible, cyclic, contractions necessary for motion. Antagonistic arrangement may initially appear inefficient, since the contraction of a muscle group stretches the antagonist one at each cycle, increasing resistance and energy consumption. We show that the nonlinear muscle mechanics is critical to the high efficiency of natural antagonistic muscle pairs, and we aim to mimic this nonlinearity via hierarchical muscle microstructure.
This talk will focus on twisted and coiled polymer actuators (TCPA). First, I will describe intriguing hierarchical super-, and hyper-coiled artificial muscles which, inspired by natural muscles, result in nonlinear J-shaped force-displacement behavior. Next, I will describe design rules to systematically select muscles for robotic mechanisms. Finally, I will describe their use to build work accumulating mechanics such as vertical rope-climbing robots.
Biography: Sameh Tawfick is a Ralph A. Andersen Scholar and Associate Professor of Mechanical Science and Engineering at the University of Illinois. He studies advanced materials, nonlinear mechanics, and manufacturing processes. Sam obtained his PhD from the University of Michigan, was a Postdoctoral Associate at the Massachusetts Institute of Technology, and a Beaufort Visiting Fellow in St. John's College at the University of Cambridge in 2023. He is the recipient of young investigator awards from the US Air Force, ASME, SME, and The Dean’s Award for Excellence in Research at Illinois. His teaching awards at the University of Illinois include The Everitt Award for Teaching Excellence, The Two-year Alumni Teaching Award, and The Engineering Council Stanley H. Pierce Award for Empathetic Student-faculty Cooperation.
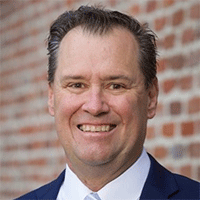
Symposium 1 Invited Speaker
Martin L. Dunn
Professor and Dean of the College of Engineering, Design and Computing
University of Colorado, Denver
Presentation Title: Tailored Actuation in 4D Printed LCE Composites via Advanced Materials and Embedded Fiber Reinforcement
Abstract: Abstract: 4D printing enables the fabrication of structures with spatially programmable, stimulus responsive material properties that can be engineered to actuate or morph in response to environmental cues. This presentation will highlight our recent work advancing 4D printing materials, manufacturing methods, and functional applications across three key areas. First, we introduce a novel two-step UV curable liquid crystal elastomer (LCE) system. Initially shaped via high-resolution vat photopolymerization techniques like digital light processing (DLP), these materials undergo a secondary thermomechanical curing step that forms an interpenetrating epoxy network, locking in mesogen alignment. By tuning the epoxy content, we can precisely adjust mechanical and actuation characteristics, enabling thermally reversible deformation for uses in active metamaterials, morphing structures, and soft robotics.
Second, we present a direct ink write (DIW) method for printing LCE composites reinforced with continuous fibers. A custom-designed print head co-deposits LCE resin and fibers, leveraging shear forces during extrusion to align mesogens within the matrix. These fiber reinforcements significantly enhance actuation force and energy absorption, while the use of conductive fibers facilitates electrothermal activation and control of composite components.
Third, we describe an embedded continuous fiber printing strategy that enhances composite quality. Fibers are printed into a vat of resin, with localized UV curing providing superior resin infiltration and geometric precision.
For each advancement, we showcase fabricated prototypes, supported by computational models that predict their responsive behaviors. Demonstrations include thermally and electrothermally actuated components for applications such as programmable metamaterials, adaptable architectures, artificial muscles, and soft robotic systems.
Biography: Martin L. Dunn is a professor and dean of the College of Engineering, Design and Computing at the University of Colorado Denver. He joined CU Denver in 2018 after serving as the founding associate provost for research at the Singapore University of Technology and Design (SUTD) where he oversaw the design and operation of the research and innovation enterprise. He was also a professor at SUTD and the founding director of the National Research Foundation-supported Digital Manufacturing and Design Center. Prior to joining SUTD, he served as a program director (mechanics of materials) in the Civil, Mechanical and Manufacturing Innovation Division at the U.S. National Science Foundation (NSF), where he was also the founding program director for the Design of Engineering Materials Systems program. He served the NSF while on leave from the University of Colorado Boulder where he was the associate dean of research in the College of Engineering, Design and Computing, chair of the Department of Mechanical Engineering and a professor of mechanical engineering, holding the Victor Schelke Endowed Chair.
Dunn's research has focused on understanding the mechanics and physics of complex heterogeneous materials through a combination of theory and experiment and using this understanding to create methods and tools to design and manufacture new materials and components. This includes constitutive modeling of the nonlinear multiphysics response (thermal, optical, mechanical) of active polymers and polymer composites, computational design automation approaches based on shape and topology optimization and additive manufacturing based on SLA, DLP and FDM technologies. Most recently this has involved the development of computational design and manufacturing methodologies for multimaterial additive manufacturing, including the creation of a technology called 4D printing – an approach that integrates new computational design, manufacturing process and materials technologies to create environmentally responsive printed components.
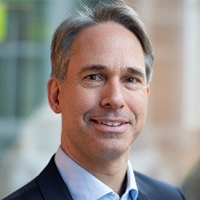
Symposium 4 Invited Speaker
Prof. Dr. Hans Peter Monner
German Aerospace Center (DLR) &
Otto-von-Guericke University of Magdeburg
Presentation Title: Demonstration and Testing of Rotating Morphing Systems at DLR
Abstract: In this presentation, we explore some advancements in rotation morphing systems, focusing on their application in in various engineering domains. We will demonstrate the active twisting mechanisms of helicopter rotor blades, highlighting how these systems enhance performance and reduce noise through adaptive aerodynamics. Additionally, we will examine the morphing trailing edge of wind turbine rotor blades, showcasing its potential to optimize energy capture and enhance fatigue life. Finally, we will delve into the design and testing of morphing fan blades in jet engines, emphasizing their role in improving fuel efficiency and reducing emissions. Through a series of experimental results and simulations, this presentation aims to illustrate the potential and challenges of rotation morphing systems on the advancement in aviation and renewable energy.
Biography: Prof. Dr. Hans Peter Monner is the head of the Department Adaptronics at the Institute of Lightweight Systems of the German Aerospace Center (DLR). Additionally, he has a professorship at the Otto-von-Guericke University of Magdeburg and gives lectures within the field of smart structures technologies, vibroacoustics and experimental mechanics. On European level his department is strongly involved in many European projects, e.g. MANTA - Movables for Next generaTion Aircraft, SABRE – "Shape Adaptive Blades for Rotorcraft Efficiency", GRETEL – "GREen Turboprop Experimental Laminar Flow Wind Tunnel Testing" or SADE "Smart High Lift Devices for Next Generation Wings". Moreover, he is involved in different international networking activities, e.g. as part of the SciTech ASTC – "Adaptive Structures Technical Committee" or the ICAST – IOC “International Organizing Committee".
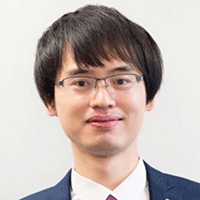
Symposium 5 Invited Speaker
Dr. Xinchang Zhang
Idaho National Laboratory
Presentation Title: Refractory Compact Heat Exchangers with Embedded Sensors Enabled by Hybrid Advanced Sintering and Additive Approach
Abstract: Structural health monitoring (SHM) of compact heat exchangers (CHXs) operating in extreme environments is essential for ensuring system reliability, safety, and longevity. This study presents the development of high-temperature sensors fabricated via aerosol jet printing (AJP) using platinum ink, selected for its exceptional thermal stability, oxidation resistance, and electrical conductivity. AJP enables precise deposition of fine-feature sensor patterns onto complex geometries, making it well-suited for integration within CHX architectures. To enhance sensor durability, an alumina-based ceramic protective layer was printed over the platinum sensing elements. The sensors demonstrated stable, repeatable performance up to 900°C during extended thermal cycling. A custom test setup was developed to evaluate sensor accuracy and robustness under steady-state and transient conditions. Substrate screening identified HG-1 ceramic-coated stainless steel as the most effective platform, offering strong adhesion and low resistance. Furthermore, electric field-assisted sintering (EFAS) was employed to embed the sensors into stainless steel 316L matrices without degrading their functionality. Post-embedding electrical tests confirmed sensor integrity, and initial characterization suggests strong potential for in-situ monitoring. EFAS was also employed to embed fiber Bragg grating sensors in structural materials for structural health monitoring. This work provides a scalable strategy for integrating high-performance temperature sensors directly into structural components, advancing embedded SHM technologies for harsh operating environments.
Biography: Dr. Xinchang Zhang is a Staff Engineer/Scientist in the Energy and Environmental Science and Technology (EES&T) directorate at Idaho National Laboratory. He is a principal investigator for multiple projects including those funded by the Department of Energy, Department of Defense, and INL Laboratory Directed Research and Development (LDRD). Zhang received his Ph.D. in mechanical engineering from Missouri University of Science and Technology in 2019. His primary focus includes advanced manufacturing (electric field-assisted sintering and additive manufacturing), advanced materials, sensors and smart structures, material characterization, and mechanical testing. Zhang authored/co-authored over 60 peer-reviewed publications and a book chapter. His current research interests include the design and fabrication of advanced materials, advanced manufacturing of compact heat exchangers, hybrid manufacturing processes for sensor embedding for structural health monitoring, processing-microstructure-property relationships, and repair and remanufacturing. He has received several awards including the Exceptional Innovation Contribution Award and Recognition Award from INL, Dean’s Ph.D. Scholar Award, Best Paper Award, NSF Travel Award, and Outstanding Reviewer for the journal Additive Manufacturing. He also serves as the reviewer for the leading journals in the area of advanced manufacturing and material science, including Nature Communications, Additive Manufacturing, Journal of Materials Science & Technology, Virtual and Physical Prototyping, Materials Science and Engineering: A, etc.
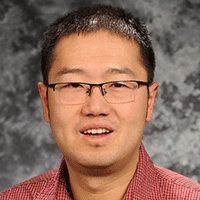
Symposium 5 Invited Speaker
Dr. Zilong Hua
Idaho National Laboratory
Presentation Title: Laser-based Non-destructive Evaluation Techniques and Their Applications in Nuclear Energy Research
Abstract: Laser metrology employs lasers to generate and detect thermal or mechanical waves in materials. By analyzing the wave propagation in materials across time, frequency, and spatial domains, thermal properties such thermal conductivity, diffusivity, and heat capacity, as well as elastic properties such as Young’s modulus and shear modulus, can be measured with high accuracy and resolution. Most laser-based measurements are remote, non-contact, and non-destructive. Therefore, with proper design and optimization, laser metrology systems can be powerful tools for non-destructive evaluation (NDE).
This talk will present the laser-based NDE systems and their applications at Idaho National Laboratory (INL). INL, under the DOE-NE, is the leading R&D national laboratory focused on the nuclear reactor design, construction, operation, and maintenance. Working within the Condensed Matter and Materials Physics group, our primary work involves fundamental research of the physical properties of nuclear fuels. Our laser metrology lab houses several thermal wave measurement systems (time-domain/frequency-domain/spatial-domain thermoreflectance, or TDTR/FDTR/SDTR, and photothermal radiometry/infrared thermography, or PTR/IRT), and laser ultrasound testing (LUT) systems (resonant ultrasound spectroscopy, or RUS, and time-domain Brillouin Scattering, or TDBS). These laser metrology NDE measurements cover spatial resolutions ranging from sub-micrometer to millimeter, and temperature from cryogenic to 1000℃. Using these systems, we investigate the thermal and elastic properties of nuclear fuels and structural materials, as well as the property change post-irradiation. These post-irradiation-examination (PIE) measurements play a crucial role in understanding the nuclear fuel performance within reactors. By collaborating with computational scientists and microstructure characterization researchers, we provide detailed insights into the performance of fuel and structural materials throughout their lifetime in reactor.
Additionally, we design and develop customized in-situ/in-operando laser metrology systems capable of collecting and analyzing data in a real-time manner, with the focus of system portability, survivability in extreme environment (such as in hot cells and reactors), and rapid screening capability. Since thermal and elastic properties are tightly tied to the microstructure defects, the real-time measurements can shed lights into the dynamic microstructure evolution. Examples include, 1) a fiber-based PTR system is used to measure real-time thermal conductivity change of nuclear fuels in MIT research reactor, 2) a lock-in IRT system is used as the real-time feedback loop to examine the manufactured part porosity in the Continuous Electric Field Assisted Sintering (CEFAS) system, and 3) an LUT system is used to monitor the annealing process of U-Zr alloys. Additional systems under development and their potential applications will also be presented.
Biography: Dr. Hua is a staff scientist at Idaho National Laboratory with research interests in the investigation of multi-scale thermal and acoustic transport phenomena of materials in extreme environment using laser-based characterization techniques. He also contributes to the development, deployment, and maintenance of state-of-art characterization techniques and INL-developed instruments, such as Thermal Conductivity Microscope (TCM) and Material Properties Microscope (MPM), for real-time, in situ measurements in reactors and hot cells, and as non-destructive evaluation tools. Dr. Hua received his doctorate in mechanical engineering at the Utah State University in 2013, and a bachelor's in materials science and engineering at the Tsinghua University (China) in 2007.
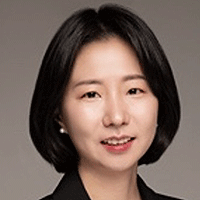
Symposium 5 Invited Speaker
Dr. Bo Mi Lee
Assistant Professor
Department of Mechanical and Aerospace Engineering
Missouri University of Science and Technology
Presentation Title: Additively Manufactured Stimuli-Responsive Materials for Wearable Sensing
Abstract: Wearable sensors are transforming healthcare, robotics, and human-machine interfaces. However, conventional sensors often suffer from rigidity, fragility, and poor conformity to dynamic surfaces such as human skin. In contrast, flexible, stimuli-responsive materials offer improved mechanical compliance, stretchability, and ability to respond to external stimuli, positioning them as viable materials for wearable sensors. Despite these advances, challenges remain in tailoring their sensing performance and scaling up fabrication. To address these challenges, additive manufacturing (AM) has emerged as a versatile approach for fabricating complex, customizable sensor architectures with minimal material waste and rapid production. Most importantly, AM enables precise control over 3D sensor geometry, porosity, and material composition, providing new opportunities to optimize sensor performance by design. In this talk, I will present our recent progress leveraging AM to assemble flexible, stimuli-responsive material-based sensors for wearable applications. The first part will focus on wireless hydrogel-based sensors for temperature and pressure monitoring. Then, I will introduce PEDOT:PSS-based flexible sensors capable of simultaneous strain and temperature sensing through piezoresistive and thermoelectric mechanisms.
Biography: Dr. Bo Mi Lee is an Assistant Professor in the Department of Mechanical and Aerospace Engineering at Missouri University of Science and Technology (Missouri S&T). Dr. Lee earned her Ph.D. in Structural Engineering from the University of California, San Diego in 2019. Following her Ph.D., she was a postdoctoral associate at the University of California, Davis (2019 – 2021), and the University of Central Florida (2021 – 2024). Dr. Lee’s research interests include multifunctional materials, stimuli-responsive nanocomposites, and data-driven approaches for advanced sensor technologies, structural health monitoring, and energy solutions.
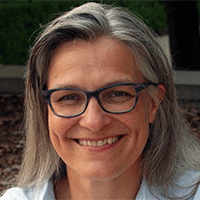
Symposium 6 Invited Speaker
Dr. Marianne Alleyne
Assistant Professor
Department of Entomology & Department of Mechanical Science and Engineering
University of Illinois at Urbana-Champaign
Presentation Title: Keeping Biologists in the Room: Addressing the Disciplinary Imbalance in Bioinspired Design
Abstract: Nature offers a vast repertoire of solutions refined through evolution, providing inspiration for novel technologies to address complex technological challenges. This bioinspired design (BID) method integrates biological insights and engineering principles. It is less common to take an opposite approach that we termed engineering-informed biology (EIB). For EIB we use engineering tools—many developed through BID—to better understand natural phenomena that motivates biological research.
The work in the Alleyne Bioinspiration Collaborative (ABCLab) focuses on the diverse movement systems and surface functionalities of insects, including dragonflies, grasshoppers, flies, cicadas, leafhoppers, and beetles. Insects have evolved in a wide range of ecological contexts, offering an array of adaptive strategies to environmental challenges. These strategies, particularly in surface properties and biomechanics, provide rich opportunities for BID. Our investigations explore phenomena such as super-hydrophobicity, antimicrobial activity, ultra-reflectivity, and latch-mediated spring actuation. These natural functionalities not only inspire engineering applications but also help us understand the evolutionary pressures that shape them, exemplifying the two-way exchange between BID and EIB.
To illustrate our approach, two case studies will be presented. The first explores the anti-microbial and hydrophobic properties of insect surfaces and their potential for technological application, such as in medical or industrial materials. These findings and fabricated surfaces can then be used to answer, for instance, mechanistic and evolutionary questions for why different insects might use different approaches for achieving multifunctionality. The second case study examines the click beetle’s jumping mechanism, driven by a latch-mediated spring actuation system, and its implications for designing compact, power-amplified mechanical systems. These mechanical system prototypes can be used to help explain the evolution for such mechanisms, which may not have been for the purpose of jumping. These examples highlight how a BID framework, informed by both biological complexity and engineering needs, can foster more effective interdisciplinary collaboration and innovation.
To effectively harness biological inspiration, especially across a broad array of systems, a structured BID framework is essential. This framework should facilitate the construction of meaningful analogies between biological functions and engineering challenges, ensuring that the most suitable biological strategies are identified and applied. BID studies remain isolated within disciplinary silos, limiting their potential impact. Interdisciplinary teams—especially those truly integrating biology and engineering—are rare but have shown greater potential for innovation. For such teams to succeed, collaboration must begin early and be sustained throughout the research process and must integrate biologists in a meaningful way. This often requires an upfront investment of time but pays dividends by aligning biological insight with engineering objectives and diverse team motivations.
Biography: Dr. Marianne Alleyne is an Assistant Professor in the Department of Entomology at the University of Illinois Urbana-Champaign. She earned her B.A. in Biology from the University of California, Berkeley (advisor: Dr. Bob Full), her M.S. in Entomology from the University of California, Riverside (advisor: Dr. Nancy Beckage), and her Ph.D. in Entomology from UIUC (advisor: Dr. Rob Wiedenmann). Her laboratory, the Alleyne Bioinspiration Collaborative (ABCLab) is particularly interested in bioinspired design (BID)—applying biological principles to solve engineering challenges, but also on engineering-informed biology (EIB), which uses engineering tools to gain insights into biological systems. Her current research focuses the development of bioinspired materials and robotics that have multi-functionality, and to use prototypes and engineering tools to help explain why certain materials and movement systems have evolved in nature.
The ABCLab fosters interdisciplinary collaboration across entomology, engineering, and design, with a strong emphasis on training undergraduate and graduate researchers. In order for both biologists and engineers to mutually benefit from BID and EID they need to know how to build, manage, and sustain collaborations that integrate diverse perspectives, methods, and goals. Only then can interdisciplinary research be innovative and lead to novel designs, while also advancing the field of biology.
Dr. Alleyne has been an active member of the Entomological Society of America (ESA) for over 25 years, serving in various leadership roles, including as ESA President in 2023. Her broader professional interests include science communication, science policy, and advancing diversity and inclusion in science.
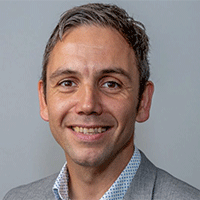
Symposium 6 Invited Speaker
Mihai "Mishu" Duduta
Assistant Professor
School of Mechanical, Aerospace and Manufacturing Engineering
University of Connecticut
Presentation Title: Soft Machines in Extreme Environments
Abstract: Soft machines—systems composed of compliant materials that mimic the adaptability and resilience of biological organisms—are redefining what is possible in environments where traditional rigid machines fail. This presentation explores the design, fabrication, and deployment of soft robotic systems engineered to operate in extreme environments, including deep underwater, outer space, and hazardous terrestrial zones. We highlight recent advances in materials science, actuation strategies, and sensing modalities that enable these machines to navigate high pressures, wide temperature ranges, corrosive conditions, and low-visibility scenarios. Through case studies, we demonstrate how softness can be a strategic advantage, enabling machines to conform, survive, and function where others cannot. This work lays the foundation for a new class of adaptive, robust, and multifunctional robots capable of thriving in the planet's—and universe's—most unforgiving environments.
Biography: Mihai "Mishu" Duduta is an assistant professor in the School of Mechanical, Aerospace and Manufacturing Engineering at UConn. He completed a BS in Materials Science and Engineering at MIT, then became the first employee of 24M Technologies, a start-up spun out to commercialize a battery technology he co-invented. His PhD thesis in soft robotics, completed at Harvard University, under the guidance of Profs. Robert Wood and David Clarke, included work which won a Gold Award at the Materials Research Society Fall Meeting 2018, and was nominated for Best Paper at ICRA 2018. Before UConn he was a Medical Devices Innovation Fellow at the University of Minnesota, then an assistant professor at the University of Toronto in Mechanical & Industrial Engineering. His research group focuses on materials and manufacturing innovations to enable soft machines to operate in extreme environments. Prof. Duduta has authored a book entitled Soft Robotics: Building Machines from Soft Matter, to be published by DeGruyter in summer 2025.
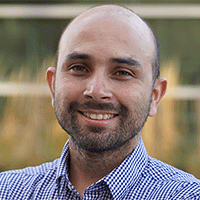
Symposium 7 Invited Speaker
Dr. Andres F. Arrieta
Full Professor of Mechanical Engineering, Aeronautics, and Astronautics Engineering (by courtesy)
Purdue University
Presentation Title: Nonlinear metamaterials for Low-frequency and Broadband Energy Harvesting
Authors: Myungwon Hwang, Sneha Srikanth, Yeongeun Ki, and Andres F. Arrieta
Abstract: Conventional resonant-based energy harvesters suffer from performance degradation when operated away from the resonant frequencies of the vibrating structures [1]. Nonlinear [2] and metamaterial-based harvesting [3] strategies have been proposed to broaden the operating bandwidths of the energy harvesters. However, the attainable bandwidth enhancements are still constrained by device or unit-cell resonances [4]. Therefore, the resulting operational frequency bandwidth in such strategies is constrained by the fundamental resonant or scattering relationships, which are inversely proportional to the building block’s size, rendering low-frequency applications particularly challenging. A new class of strongly nonlinear interactions in metamaterials that sustain soliton propagation can provide a route to address this bandwidth limitation [5]–[7]. The particle-like nature of solitons offers a fundamentally different mechanism to achieve effective dynamics that break the strong link between unit cell size and operating frequency [8], [9].
We present a class of multistable metastructures displaying strong nonlinear interactions from propagating topological solitons or transition waves enabling low-frequency and broadband energy harvesting. We show how transition waves excite the same type of response in the metastructure’s units regardless of the input excitation. The invariance of these dynamics allows for achieving robust impedance matching between the mechanical and electrical responses, thereby resulting in efficient electromechanical energy transduction. We also present a new dynamic phenomenon referred to as solitonic resonance, in which soliton-structural mode interactions enable multistable metastructures to exhibit extreme input-output energy exchange. By tuning the topology of our multistable metastructures, we can convert the input's frequencies into output responses that are orders of magnitude apart. These soliton-driven nonlinear interactions break the dependence of the attainable unconventional dynamical properties on the unit cell's size in resonance- or scattering-based metamaterials. The investigated multistable metastructures’ dynamics provide a route to accelerating metamaterials adoption for energy harvesting in structural applications by enabling low-frequency operation.
Acknowledgements: We gratefully acknowledge the support of the National Science Foundation (Grant No. CMMI-1935137) funding this research.
References
[1] N. G. Stephen, "On energy harvesting from ambient vibration," J. Sound Vib., vol. 293, no. 1–2, pp. 409–425, 2006.
[2] L. Gammaitoni, I. Neri, and H. Vocca, "Nonlinear oscillators for vibration energy harvesting," Appl. Phys. Lett., vol. 94, p. 164102, 2009.
[3]Z. Chen, B. Guo, Y. Yang, and C. Cheng, "Metamaterials-based enhanced energy harvesting: A review," Phys. B Condens. Matter, vol. 438, no. 0, pp. 1–8, 2014, doi: 10.1016/j.physb.2013.12.040.
[4] S. Gonella, A. C. Tob, and W. K. Liu, "Interplay between phononic bandgaps and piezoelectric microstructures for energy harvesting," J. Mech. Phys. Solids, vol. 57, no. 3, pp. 621–633, 2009, doi: 10.1016/j.jmps.2008.11.002.
[5]M. Hwang and A. F. Arrieta, "Input-Independent Energy Harvesting in Bistable Lattices from Transition Waves," Sci. Rep., vol. 8, no. 1, p. 3630, Dec. 2018, doi: 10.1038/s41598-018-22003-7.
[6] M. Hwang and A. F. Arrieta, "Solitary waves in bistable lattices with stiffness grading: Augmenting propagation control," Phys. Rev. E, vol. 98, no. 4, p. 042205, Oct. 2018, doi: 10.1103/PhysRevE.98.042205.
[7] M. Hwang and A. F. Arrieta, "Extreme Frequency Conversion from Soliton Resonant Interactions," Phys. Rev. Lett., vol. 126, no. 7, p. 073902, Feb. 2021, doi: 10.1103/PhysRevLett.126.073902.
[8] M. Hwang and A. F. Arrieta, "Energy harvesting characteristics in metamaterials based on bistable lattices," in Active and Passive Smart Structures and Integrated Systems XII, 2019, no. May, p. 13, doi: 10.1117/12.2514426.
[9] M. Hwang and A. F. Arrieta, "Topological wave energy harvesting in bistable lattices," Smart Mater. Struct., vol. 31, no. 1, p. 015021, 2022, doi: 10.1088/1361-665x/ac37ff.
Biography: Dr. Andres F. Arrieta is a Full Professor of Mechanical Engineering and Aeronautics and Astronautics Engineering (by courtesy) at Purdue University, where he leads the Programmable Structures Lab. Previously, he worked as a Group Leader at ETH Zurich's CMAS Lab and as a Research Associate at the Dynamics and Oscillations Group at TU Darmstadt. He received his Ph.D. in Mechanical Engineering from the University of Bristol and his BEng from the Los Andes University, Bogota, Colombia.
Dr. Arrieta’s research in structural mechanics investigates the fundamental interaction between geometry, hierarchy, and nonlinearity and their role in designing systems with intrinsic properties enabling adaptation, autonomy, and environmental responsiveness. Current efforts concentrate on the modeling and designing of morphing structures, soft robotics, embodied intelligence in structures, nonlinear metamaterials, energy harvesting, and bioinspired design. The Programmable Structures Lab's work has been highlighted by several media outlets, including National Geographic and Nature's News and Views.
His research has been recognized with several research awards, including the 2021 inaugural Early Career Award in Smart Materials and Structures (IOP Science); NSF CAREER Award (2020); the American Society of Heating, Refrigerating and Air-Conditioning Engineers (ASHRAE) Innovation Research Grant; the ASME Gary Anderson Award (2018) for "outstanding contributions to the field of Adaptive Structures;" and the ETH Postdoctoral Fellowship (2012).

Symposium 7 Invited Speaker
Dr. Mohammad H. Malakooti
Assistant Professor of Mechanical Engineering
University of Washington – Seattle
Presentation Title: Stretchable Thermoelectric Wearables with 3D Soft Architectures and Electrical Self-Healing
Abstract: Designing thermoelectric generators that are simultaneously stretchable, efficient, and durable remains a major challenge for energy-harvesting wearables. In this talk, I will present a new class of stretchable thermoelectric devices built using 3D soft architectures that integrate multifunctional elastomer composites, rigid semiconductors, and electrically self-healing liquid metal conductors. These devices operate reliably under extreme mechanical deformation up to 230% strain and exhibit high power density at low temperature gradients. I will describe how 3D printing is used to fabricate the thermoelectric modules and enhance thermal management through engineered infill patterns. This approach helps maintain the temperature gradient across the semiconductors, increasing energy conversion without compromising mechanical flexibility or resilience. The devices demonstrate high damage tolerance, continuing to function after multiple punctures and thousands of stretching cycles. They also provide effective active heating and cooling through the Peltier effect, enabling on-demand thermoregulation. When integrated with 3D-printed heatsinks, they can power LEDs and sensors by harvesting body heat, which highlights their potential for self-powered, skin-conformable electronics. I will conclude by discussing how machine learning can accelerate the design of soft multifunctional composites, particularly for flexible thermoelectric devices.
Biography: Dr. Mohammad H. Malakooti is an Assistant Professor of Mechanical Engineering at the University of Washington – Seattle. He leads the iMatter Lab, a research group dedicated to creating materials that match the extraordinary adaptability, rich multifunctionality, and embodied intelligence of natural material systems. He received his Ph.D. from the University of Florida in 2015, completed a Postdoctoral Fellowship at the University of Michigan (2015–2017), and was a Research Scientist at Carnegie Mellon University (2017–2019). Dr. Malakooti has published over 45 peer-reviewed articles in leading scientific journals. His contributions have been recognized with several honors, including ASME Best Paper Awards (2016, 2022) and the Outstanding Postdoctoral Fellow Award from the University of Michigan.
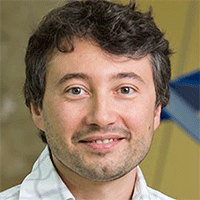
Special Symposium Invited Speaker
Dr. Mattia Gazzola
Charles Conrad Kritzer Associate Professor
University of Illinois Urbana-Champaign
Presentation Title: Modeling, Realization and Control of Living Creatures, Machines, and Materials
Abstract: Fiber-based organization of matter is pervasive in nature and engineering, in active and passive settings, and across scales, from muscles, tendons and bones that make up full organisms to polymers, composite materials, and soft robots. Here a modeling approach based on assemblies of Cosserat rods is presented to tackle fibrous systems that are distributed, heterogeneous, and hierarchically organized. Scalability, robustness, and utility of our simulation methods are then demonstrated for the design, realization and control of soft living creatures, bio-hybrid machines, and metamaterials.
Biography: Mattia Gazzola is the Charles Conrad Kritzer Associate Professor in the Mechanical Science and Engineering Department at the University of Illinois Urbana-Champaign. He joined UIUC in Fall 2016 after a postdoc at Harvard and a PhD at ETH Zurich. His work lies at the interface between mechanics, biology, robotics, and computing. His studies were awarded with the ETH Medal, Early and Advanced Swiss National Science Foundation Fellowships, NSF CAREER, and featured on the cover of several scientific journals including Science, Nature, PNAS, PRL. He is the Lead PI and co-director of the center-scale NSF Expedition "Mind in Vitro–Computing with Living Neurons".
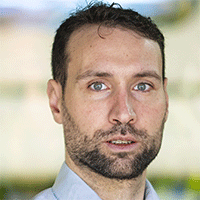
Special Symposium Invited Speaker
Marc Serra-Garcia
Tenure Track Group Leader
AMOLF, 1086VA Amsterdam, the Netherlands
Presentation Title: Physical Computing with Metamaterials
Abstract: There is a significant range of physical phenomena—from nonlinear elasticity, to symmetry, noise, topology, and disorder — that are rarely utilized in traditional computing paradigms. Yet these phenomena can unlock new efficiencies, by directly processing signals in their natural domain, and by bypassing the traditional abstraction stack associated with digital CMOS technology. However, building physical computers is challenging. Information processing tasks generally involve complex input-output relations, thus requiring designs that are highly expressive; and for these designs, the relation between function and structure is nontrivial, complicating the simulation, design, and fabrication of devices. In my talk, I will illustrate our journey towards using metamaterials for physical computing, with two recent examples. First, I will talk about our results in passive speech recognition, where we leverage a phononic metamaterial to implement wake-up-word detection with zero standby power consumption. Second, I will discuss our ongoing work in self-learning materials, that autonomously adapt to improve their performance—driven by their ability to form long-term memories in response to examples and external feedback.
Biography: Marc Serra-Garcia (Manresa, 1987) is a tenure-track group leader at the AMOLF research institute in Amsterdam. After a BSc in Physics at Universitat Autònoma de Barcelona, he did a MSc degree at Caltech, and a PhD at ETH Zurich. His research is currently focused on novel (beyond-CMOS) approaches to information processing, with the goal of using a richer and more diverse set of physical phenomena to implement relevant information-processing tasks with low power. The research has been recognized by an ERC Starting grant, and various other grants from the Dutch Research Council and Swiss National Science Foundation.