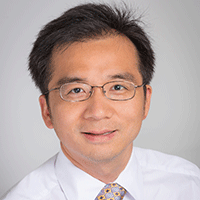
Wednesday, November 1, 2023, 9:45AM – 10:30AM
Name: Tony Jun Huang
Presentation Title: Acoustofluidics: Merging Acoustics and Fluid Mechanics for Biomedical Applications
Abstract: The use of sound has a long history in medicine. Dating back to 350 BC, the ancient Greek physician Hippocrates, regarded as “the father of medicine”, devised a diagnostic method for detecting fluid in the lungs by shaking patients by their shoulders and listening to the resulting sounds emanating from their chest. As acoustic technology has advanced, so too has our ability to “listen” to the body and better understand underlying pathologies. The 18th century invention of the stethoscope allowed doctors to gauge the health of the heart; the 20th century invention of ultrasound imaging revolutionized the field of biomedical imaging and enabled doctors to diagnose a range of conditions in the fields of obstetrics, emergency medicine, cardiology, and pulmonology. In the last decade, a new frontier in biomedical acoustic technologies has emerged, termed acoustofluidics, which joins cutting-edge innovations in acoustics with micro- and nano- scale fluid mechanics. Advances in acoustofluidics have enabled unprecedented abilities in the early detection of cancer, the non-invasive monitoring of prenatal health, the diagnoses of traumatic brain injury and neurodegenerative diseases, and have also been applied to develop improved therapeutic approaches for transfusions and immunotherapies. In this talk, I summarize our lab’s recent progress in this exciting field and highlight the versatility of acoustofluidic tools for biomedical applications through many unique examples, ranging from the development of high-purity, high-yield methods for the separation of circulating biomarkers such as exosomes and circulating tumor cells, to highly precise, biocompatible platforms for manipulating cells and studying cell-cell communication, to high-throughput therapeutic approaches for platelet isolation and enrichment, to strategies for high-resolution 3D bioprinting, to programable, contact-free technologies for digital fluid manipulation. These acoustofluidic devices can precisely manipulate objects across 7 orders of magnitude (from a few nanometers to a few centimeters). Thanks to these favorable attributes (e.g., versatility, precision, and biocompatibility), acoustofluidic devices harbor enormous potential in becoming a leading technology for a broad range of applications, playing a critical role for translating innovations in technology into advances in biology and medicine.
Bio: Tony Jun Huang is the William Bevan Distinguished Professor of Mechanical Engineering and Materials Science at Duke University. Previously he was a professor and the Huck Distinguished Chair in Bioengineering Science and Mechanics at The Pennsylvania State University. He received his Ph.D. degree in Mechanical and Aerospace Engineering from the University of California, Los Angeles (UCLA) in 2005. His research interests are in the fields of acoustofluidics, optofluidics, and micro/nano systems for biomedical diagnostics and therapeutics. He has authored/co-authored over 260 peer-reviewed journal publications in these fields. His journal articles have been cited more than 29,000 times, as documented at Google Scholar (h-index: 91). He also has 26 issued or pending patents. Prof. Huang was elected a fellow (member) of National Academy of Inventers (USA) and the European Academy of Sciences and Arts. He was also a fellow of the following six professional societies: American Association for the Advancement of Science (AAAS), the American Institute for Medical and Biological Engineering (AIMBE), the American Society of Mechanical Engineers (ASME), the Institute of Electrical and Electronics Engineers (IEEE), the Institute of Physics (UK), and the Royal Society of Chemistry (UK). In addition, he has selected to receive many prestigious awards and honors including a 2010 National Institutes of Health (NIH) Director's New Innovator Award, a 2012 Outstanding Young Manufacturing Engineer Award from the Society for Manufacturing Engineering, the 2014 IEEE Sensors Council Technical Achievement Award from the Institute of Electrical and Electronics Engineers (IEEE), the 2017 Analytical Chemistry Young Innovator Award from the American Chemical Society (ACS), the 2019 Van Mow Medal from the American Society of Mechanical Engineers (ASME), and the 2019 Technical Achievement Award from the IEEE Engineering in Medicine and Biology Society (EMBS). In 2022, he was named to a global list of the most highly cited researchers (cross field) by Clarivate (Web of Science).
Thursday, November 2, 9:15AM – 10:00AM
Name: Alexander F. Vakakis
Presentation Title: Engineering Intentional Nonlinearity in Acoustics and Phononics
Abstract: We explore the intentional implementation of strong nonlinearity in acoustical and phononic waveguides, with the aim of enabling passive targeted energy transfer (TET) and management in these systems This is a predictive engineering approach whereby externally induced or self-excited broadband/narrowband energy, is either irreversibly directed in preferential paths/modes, rapidly scattered in the frequency/wavenumber domains, dissipated locally, or harvested at a priori designated sites. Interestingly, such directed energy transfers and management mimic analogous irreversible energy cascades in Nature, e.g., in turbulent flows or granular assemblies, and, as such, benefit from the well-known robust and enhanced dissipative features exhibited by these natural phenomena. Our approach dictates advanced theoretical modelling and analysis to account for strongly nonlinear effects, robustness studies to avoid unwanted instabilities and/or unaccounted complexity in the acoustics, but also nonlinear system identification, reduced-order modelling, optimization, and experimental validation of theoretical predictions and deigns. Unique benefits of this nonlinear approach include passive tunability of the acoustics to energy and frequency/wavelength contents of the applied excitations, as well as, drastic and beneficial changes in the global system acoustics by means of the addition of local nonlinear elements. We discuss applications such as directional wave transmission in phononic lattice networks; interband TET in phononic systems; passive ways for breaking acoustic reciprocity in acoustic waveguides with local nonlinearities and asymmetries; nonlinear topological insulators; and granular shock protectors with time-scale disparity in their responses – that is, with the capacity to respond either in the dynamic or the acoustic range depending on the location of the external shock. The aim is to translate this approach to new methods, technologies, applications and devices that exploit and showcase intentional strong nonlinearity.
Bio: Alexander F. Vakakis received his Ph.D. from Caltech (1990), M.Sc. from Imperial College, London, UK (1985), and Diploma in Mechanical Engineering from the University of Patras, Greece (1984). Currently he is the Donald Biggar Willett Professor of the College of Engineering of the University of Illinois at Urbana – Champaign (UIUC) where he co-directs the Linear and Nonlinear Dynamics and Vibrations Laboratory; moreover, he is co-affiliate faculty at the University of Stuttgart, Germany. Among other awards, he is the recipient of the Tau Beta Pi Daniel C. Drucker Eminent Faculty Award from the UIUC College of Engineering (2023), an Alexander von Humboldt Research Award (2019), the Edmond J. Safra Visiting Professorship from Technion (2019), and the ASME Thomas K. Caughey Award in nonlinear dynamics (2014). He has published over 350 archival journal publications, holds four patents, and has authored or edited 6 technical texts and monographs. Many of his PhD students and postdoctoral fellows are currently faculty members in the US and abroad, and researchers in R&D centres. His research interests include nonlinear dynamics, vibrations, and acoustics from the macro- to the micro-scales, passive energy management and targeted energy transfer, nonlinear phononics, acoustic metamaterials, nonlinear system identification, bioengineering, non-smooth dynamics and vibration energy harvesting.