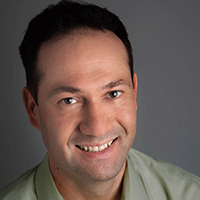
Panel Summary: The emergence of 5G will help power a significant rise in wearable/mobile/wireless communication, providing the infrastructure needed to carry large amounts of data, allowing for a smarter connected world. A panel of experts from diverse industrial sectors and academia will share their vision on the future of small to large wearable/wireless electronics thermal management and other advanced system-level thermo-mechanical challenges and solutions of the future.
Moderator: Dr. Victor Chiriac, Managing Director of Global Cooling Technology Group, ASME Fellow
A fellow of the American Society of Mechanical Engineers (ASME) since 2014, Dr. Victor Adrian Chiriac is a co-founder and managing partner with the Global Cooling Technology Group since 2019. He previously held technology/engineering executive/leadership roles with Motorola (1999-2010), Qualcomm (2010 - 2018) and Huawei R&D USA (2018 - 2019). Dr. Chiriac was elected Chair of the ASME K-16 Electronics Cooling Committee (2013-2017), also elected the Arizona and New Mexico IMAPS Chapter President in 2010. He is a leading member of the organizing committees of ASME/InterPack, ASME/ IMECE and IEEE/CPMT ITherm Conferences, also a co-editor of the popular Electronics Cooling magazine. He holds 19 U.S. issued patents, 2 US Trade Secrets and 1 Defensive Publication, and has published over 107 papers in scientific journals and at conferences.
Panelists
- Dr. Todd Salamon, Nokia Bell Labs, Member of Technical Staff
- Dr. YC Lee, Kelvin Thermal, President and CEO
- Prof. Yogendra Joshi, Georgia Institute of Technology
- Dr. Ravi Mahajan, Intel Fellow
- Prof. John R. Thome, GCTG, Technical Director
- Ryoson Hiroyuki, Dexerials/ex Sony Chemicals, Chief Executive Engineer
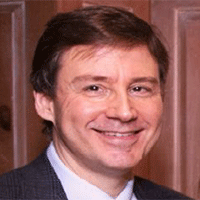
Dr. Todd Salamon, Nokia Bell Labs
Talk Title: Impact of 5G on Thermal Management of Telecommunications Networks
Abstract: Network operators are beginning the buildout of 5G wireless networks, with the enhanced bandwidth and extremely low latency of 5G networks anticipated to enable a range of applications, including self-driving cars, industrial automation, and digital health, to name a few. The demands that 5G applications will place on network infrastructure require continued innovations in wireless and wireline technologies. As one example, the low latency requirements of 5G-enabled applications is resulting in the emergence of so-called “edge” computing, where compute and data resources are located in small-scale data centers that are near the end user or application, with high-speed radio access networks (RANs) providing the needed application bandwidth. In this talk, I will discuss telecom industry trends brought on by 5G, how such trends are impacting the design of networks and devices, and the associated implications for thermal management in telecommunications networks.
Biography: Todd R. Salamon received the Ph.D. degree in chemical engineering from the Massachusetts Institute of Technology (MIT), Cambridge, MA, USA. He is currently a Member of Technical Staff in the Hybrid Integration Research Group, Nokia Bell Labs, Murray Hill, NJ, USA, where he has worked on thermal management, microfluidics, transport phenomena in optical fiber manufacturing, design of photonic crystal fibers, and Raman and erbium amplifier dynamics and control in transparent optical networks. He has authored over 60 publications and conference presentations and holds 36 issued or pending patents. He was the Principal Investigator on a U.S. Department of Energy project titled “Advanced Refrigerant-based Cooling Technologies for the Information and Communications infrastructure” to develop and commercialize refrigerant-based cooling technology targeting the Information and Communications Technology (ICT) sector, and a Team Member of the MIT-lead DARPA ICECool Fundamentals Program.
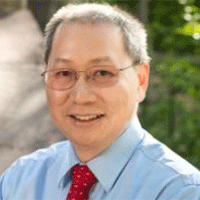
Dr. Y.C. Lee, Kelvin Thermal
Talk Title: Foldable Thermal Ground Planes
Abstract: Foldable thermal ground planes (TGPs) are enabling components for more powerful foldable smartphones, laptop PCs, ARs/VRs, and other systems with varying configurations in real time. We will present testing results on our foldable TGPs with a bending radius of 3mm and 150,000 folding cycles. More importantly, we will illustrate how to improve foldable system’s power dissipation by at least 3X with the use of the foldable TGPs.
Biography: Dr. Y. C. Lee is the President and CEO of Kelvin Thermal. He is retired from the University of Colorado Boulder in August 2021. Dr. Lee received the ASME InterPACK Achievement Award in 2013. He was the Editor of ASME Journal of Electronic Packaging from 2015 to 2020.
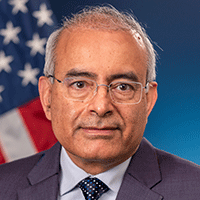
Prof. Yogendra Joshi, Georgia Tech
Talk Title: Microfluidic Thermal Management for Heterogeneously Integrated Microsystems
Abstract: Heterogeneous integration is bringing in several thermal challenges. Two examples will be presented to illustrate these and some potential solutions. Power delivery to high performance computing hardware requires internal voltage regulators (IVR), which employ package embedded passive elements such as inductors. Close proximity of the passives and IVR requires independent thermal management of the passives. The passives are embedded within the packaging structure and do not have direct access to thermal management. The second example considers glass interposer based packaging of 5G and beyond mm wave wireless modules. Embedding of components within the interposer is a promising technology for compact heterogeneous integration. Thermal management of components such as power amplifiers for glass interposer based packaging presents significant challenges. As discussed, microfluidics presents promising solutions for both applications.
Biography: Yogendra Joshi is Professor and John M. McKenney and Warren D. Shiver Distinguished Chair at the G.W. Woodruff School of Mechanical Engineering at the Georgia Institute of Technology. His research interests are in multi-scale thermal management. He is the author or co-author of over four hundred publications in this area, including over two hundred journal articles. He is an elected Fellow of the ASME, the American Association for the Advancement of Science, and IEEE.
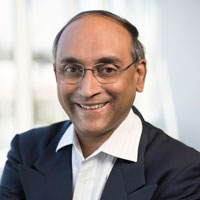
Dr. Ravi Mahajan, Intel Corp.
Talk Title: Thermal Management in Devices in Thermally Demanding Environments
Abstract: The context for the thermal problem for some of the devices and applications addressed by this panel is provided. A call for action on developing thermal solutions is made and opportunities for collaboration are identified.
Biography: Ravi Mahajan is an Intel Fellow responsible for Assembly and Packaging Technology Pathfinding for future silicon nodes. Ravi also represents Intel in academia through research advisory boards, conference leadership and participation in various student initiatives. He has led Pathfinding efforts to define Package Architectures, Technologies and Assembly Processes for multiple Intel silicon nodes including 90nm, 65nm, 45nm, 32nm, 22nm and 7nm silicon. Ravi joined Intel in 1992 after earning Ph.D. in Mechanical Engineering from Lehigh University. He holds the original patents for silicon bridges that became the foundation for Intel’s EMIB technology. His early insights have led to high-performance, cost-effective cooling solutions for high-end microprocessors and the proliferation of photo-mechanics techniques for thermo-mechanical stress model validation. His contributions during his Intel career have earned him numerous industry honors, including the SRC’s 2015 Mahboob Khan Outstanding Industry Liaison Award, the 2016 THERMI Award from SEMITHERM, the 2016 Allan Kraus Thermal Management Medal & the 2018 InterPACK Achievement award from ASME, the 2019 “Outstanding Service and Leadership to the IEEE” Awards from IEEE Phoenix Section & Region 6 and most recently the 2020 Richard Chu ITherm Award For Excellence and the 2020 ASME EPPD Excellence in Mechanics Award. He is one of the founding editors for the Intel Assembly and Test Technology Journal (IATTJ) and currently VP of Publications & Managing Editor-in-Chief of the IEEE Transactions of the CPMT. He has long been associated with ASME’s InterPACK conference and was Conference Co-Chair of the 2017 Conference. Ravi is a Fellow of two leading societies, ASME and IEEE.
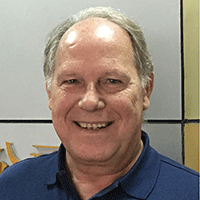
Professor John R. Thome, GCTG LLC
Talk Title: Pulsating Heat Pipe for Cooling of Mobile Electronics
Abstract: Pulsating heat pipes (PHPs) are a new high performance cooling solution for mobile electronics: tablets, phones, portable PCs, etc. Presently, a newly developed planar PHP has been developed with a very thin form factor (< 1.0mm thickness) that handles one or multiple distributed thermal cooling loads up to and beyond 30W. Some test results and IR thermal images will be presented to illustrate the thermal performance in various cooling orientations (vertical and horizontal) and in steady-state/transient operation..
Biography: John R. Thome is Co-Founder and Technical Director of Global Cooling Technology Group in Phoenix, AZ developing pulsating heat pipe technologies for the mobile and commercial electronics market as well as JJ Cooling Innovation in Lausanne, Switzerland, a micro-two-phase cooling technology development company for numerous other industries. Has 20+ years of experience with development of micro-two-phase cooling systems for electronics (pumped systems, thermosyphons, pulsating heat pipes and high fidelity simulators for them). He is the author of five books and is editor-in-chief of the Encyclopedia of Two-Phase Heat Transfer and Flow (16 volumes). He received the 2017 Nusselt-Reynolds Prize, the 2019 IEEE ITHERM Award and the 2019 ASME InterPack Medal, the ASME Heat Transfer Division's Journal of Heat Transfer Best Paper Award in 1998, the United Kingdom’s Institute of Refrigeration J.E. Hall Gold Medal in 2008, the 2010 ASME Heat Transfer Memorial Award, among others.

Hiroyuki Ryoson, Dexerials (ex-Sony Chemicals)
Talk Title: Low Thermal Resistance 3D Stacked IC Using WOW Technology
Abstract: Recently stacked DRAM is commercialized in response to the demand for increasing DRAM capacity, and it uses microbump technologies for stacking. When using microbump method, the thermal resistance in interlayer and in BEOL are large, so that total thermal resistance is larger. As the result total the temperature rise between top layer and bottom layer of stacked dies is large. At this point Tokyo institute of Technology reports the bumpless stacking technologies. When this method is used via last technology and the total thermal resistance is small, the temperature rise is also small. The total thermal resistance in microbump method is 1.54 K/W and the temperature rise at 22.6 W input power is 19.9 C. On the other hand, the total thermal resistance method in bumpless method is only 0.46 K/W and the temperature rise at 22.6 W input power is only 5.8 C.
Biography: Hiroyuki Ryoson is the Dexerials Executive Chief Engineer responsible for thermal management technology and thermal management materials. Ryoson is also a researcher of Tokyo Institute of Technology responsible 3D stacking technology development. He was also a member of Sony corporation responsible for thermal management technology development.