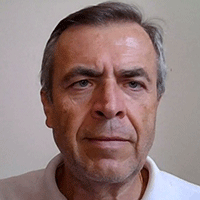
Monday, August 21; 8:00am - 9:00am
Professor Primo Zingaretti
Università Politecnica delle Marche
Italy
Presentation Title: VRAI: a Journey on Artificial Intelligence Techniques for Mechatronics and Embedded Systems, from Vision Robotics to Virtual Reality
Abstract: VRAI is the name/acronym of the Vision, Robotics and Artificial Intelligence Laboratory at the Department of Information Engineering (DII) of the Università Politecnica delle Marche. Founded about 20 years ago, its researchers have experienced all the rapid advances made by technology in autonomous, intelligent, mechatronics and embedded systems. This keynote, after briefly delineating the path followed, will present, based on several application cases, the integration of Artificial Intelligence techniques within Cyber Physical Systems, shedding light on its profound implications for autonomous decision-making capabilities. We will analyze how AI, combined with sensors and IoT, enables systems to learn, adapt, and respond, thereby pushing the boundaries of automation and control in mechatronic systems. Lastly, we will introduce and elaborate on the concept of Digital Twins and their transformative role in the field. By providing real-time, dynamic replicas of physical systems, Digital Twins allow us to foresee and optimize system performance, leading to unprecedented levels of efficiency and adaptability, aso in term of Human Interaction on immersive XR environment.
Biography: Primo Zingaretti is a Full Professor of Computer Engineering at the Department of Information Engineering (DII) at the Università Politecnica delle Marche, where he currently teaches "Computer Graphics and Multimedia", "Information Processing Systems" and "Information Technology for Cultural Heritage".
His research activity has involved several aspects, both theoretical and applicative, being Artificial Intelligent Systems (Artificial Intelligence), in particular, systems interacting with the surrounding environment mainly through visual sensors (Computer Vision), the unifying research direction. Regarding the theoretical aspects, the research has been oriented to the study of two main problems: - definition and development of techniques and efficient data structures for the representation and processing of images (Pattern Recognition, Image Processing and Understanding); - definition and development of frameworks for machine vision, graphics and multimedia systems that incorporate machine learning capabilities (Decision Support Systems, Machine Learning and Deep Learning).
The main application areas involved have been: i) Robotic Vision, for the self-location and autonomous navigation of mobile robots (Mobile Robotics) of land (Unmanned Ground Vehicle - UGV), water (Unmanned Undersea Vehicle - UUV) or air (Unmanned Aerial Vehicle - UAV) and scene monitoring; ii) Mechatronic systems, embedded systems and, in particular, Cyber Physical Systems in industry 4.0, exploiting different technologies/sensors for data acquisition (e.g., RGB-D, beacon BLE, IoT), different Real-Time Locating Systems for the localization of objects/persons (e.g., RFID, UWB) and Human Behaviour Analysis, in particular, for customer profiling in retail and home automation systems for Ambient Assisted Living; iii) Geomatic applications, for the automatic classification of heterogeneous data in the production of themes (GIS-ready automatic cartography) and in the monitoring of environments/products, in particular in Precision Farming, from the automatic interpretation of remote sensing data from satellite and/or UAV equipped with innovative image acquisition systems, both multi-spectral and hyper-spectral, as well as ground acquired; iv) Extended Reality (XR), including Augmented Reality (AR) and Virtual Reality (VR), systems in the fields of cultural heritage, tourism, industry 4.0 and medicine.
Great attention has been directed to the technological transfer of research results. In particular, he was a founding partner of two university spin-offs and a specific interest was devoted to industrial applications and factory automation, being scientific and/or technical responsible for many national and international research projects, funded by private companies or by public bodies.
He has been one of the Promotors (and still a member of the Conference Board) of the European Conference on Mobile Robots – ECMR, the Program Chair of ECMR 2003, Radziejowice/Warsaw, Poland and the General Chair of ECMR 2005, Ancona, Italy, General Chair of IEEE/ASME Mechatronic and Embedded Systems and Applications - MESA'11, Washington DC, USA and IEEE/ASME MESA'14, Senigallia, Italy as well as the Program Chair of IEEE/ASME MESA'10, Qingdao, China. He has been Director of the first (PSFMR'05) and second (PSFMR'06) International School on Perception and Sensor Fusion in Mobile Robotics, held with the support of the EURON - European Robotics Research Network of Excellence, for doctoral or post-doctoral students, Chair of the Technical Committe MESA "Mechatronic and Embedded System Applications" of the ASME Design Engineering Division (DED) 2010-2011, and Founder and Director of the Laboratory of Vision, Robotics and Artificial Intelligence (VRAI) at the Department of Information Engineering (DII) of the Università Politecnica delle Marche, which is currently composed of some 30 researchers (faculty, PhD and PhD students) engaged in numerous European, national and regional collaborations and research projects.
He has been Guest Editor of special issues and author or co‐author of more than 200 scientific papers in journals, book chapters or conference proceedings. He is Senior Member of IEEE, member of ASME, promoter of AIxIA, Vice President of CVPL.
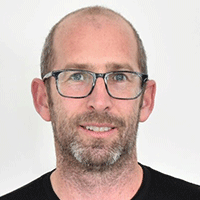
Tuesday, August 22; 8:10am - 9:10am
Professor Chris Pretty
University of Canterbury
New Zealand
Description: Healthcare costs are increasingly unaffordable in New Zealand and internationally, and are only going to get worse over the next 20-50 years with the ageing population. To avoid rationing and increased inequity in healthcare, we need to be more efficient and effective at delivering health services.
Mechatronics engineering can enable efficient and effective healthcare systems through lower cost technology, better use of models and data for improved diagnosis, monitoring, and therapy. Right now, we are at an amazing technological confluence of high performance, low-cost processing, connectivity, and components, all in a small physical size, coupled with rapid, accurate, low-cost digital manufacturing systems. We can now solve problems in a way that could not have even been imagined 20-years ago. But, to achieve these goals, we need to enable interoperability, data sovereignty, and new business models.
This talk explores some of the challenges and potential solutions to improving efficiency, efficacy, and equity of healthcare using mechatronics engineering, with some examples from my own research experience.
Biography: Professor Chris Pretty is currently a co-director of the Mechatronics Engineering program in the Department of Mechanical Engineering at the University of Canterbury, New Zealand.
His primary field of research is the application of engineering to solve problems in medicine, principally in critical care and rehabilitative robotics. Specifically, his research involves the modelling, sensing, control, and actuation of dynamic physiological systems, and this forms the common thread between diverse areas of application.
Prof. Pretty's research has particular emphasis on using physiological models to synthesise and "add value" to new or existing sensor data to enable improved care for patients through improved monitoring, diagnosis, and control, as well as reduced cost and effort for clinicians.
Prof. Pretty completed a PhD in Bioengineering in 2012 at the University of Canterbury, NZ. Following his PhD, he moved to Belgium as a postdoctoral researcher at the University of Liege in the GIGA Cardiovascular Sciences research group. He is a past chair of the ASME/IEEE Mechatronics and Embedded Systems and Applications Technical Committee.