SUNDAY, AUGUST 17 | 6:30pm–7:30pm | Huntington B
Description:The CIE Division is hosting a one-hour networking event at the 2025 IDETC-CIE on Sunday, August 17, from 6:30 PM to 8:00 PM, including a reception. This event is designed to recognize the contributions of those from nontraditional backgrounds in engineering, celebrate achievements within the ASME community, and foster professional networking and mentorship opportunities.
The event will be kicked off by Tom Costabile, Executive Director of ASME. It will feature a group of panelists with expertise in emerging technologies—such as Modeling and Simulation, Digital Twins, Machine Learning, and Artificial Intelligence-and how these innovations are helping to broaden access and opportunity across the field. This event is open to all.
Moderator
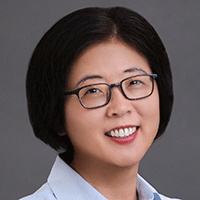
Dr. Christina Wang serves as Vice President of Engineering Applications at the American Bureau of Shipping (ABS), where she plays a pivotal role in supporting safety, regulatory compliance, and digital innovation within the marine and offshore industries. Her journey from a Ph.D.-trained expert in classical naval architecture to a forward-thinking executive in emerging technologies reflects both her professional evolution and her enduring commitment to the global maritime community.
Dr. Wang earned her Ph.D. in Marine Structures from the Norwegian University of Science and Technology. She is a Fellow of both the American Society of Mechanical Engineers (ASME) and the Society of Naval Architects and Marine Engineers (SNAME). In addition to her technical and leadership credentials, she has completed the Stanford Executive Program and holds an Executive Certificate in Management and Leadership from MIT. Dr. Wang is also a member of the ASME CIE Executive Committee.
Panelists
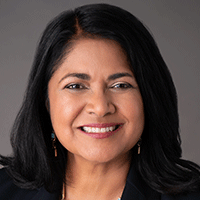
Dr. Uma Jayaram is a distinguished technology executive and board member with expertise in technology innovation and AI-driven business strategy. As the GM of EA PAIR, she leads global academic partnerships with worldwide studios for Electronic Arts, a leading $37B entertainment company. Previously, Uma served as GM of EA's Applied Research and Innovation division, managing teams across Europe, Canada, and the USA.
Uma began her career as a Professor at Washington State University. During that period, she co-founded three companies with her students and colleagues, successfully selling one to Intel in 2016. At Intel, she served as the Managing Director of the IPX Engineering team, delivering the groundbreaking VR experience at the 2018 Winter Olympics in PyeongChang.
An ASME Fellow, Uma has been recognized for her impactful contributions to engineering design, entertainment, manufacturing, aerospace, and gaming. She has published over 60 peer-reviewed articles, holds seven patents, and is a sought-after speaker at prestigious forums such as TEDx, IEEE, and MIT Tech Review. In 2024, she was inducted into Virginia Tech’s Academy of Engineering. Uma holds Ph.D. and M.S. degrees in mechanical engineering from Virginia Tech and holds a BTech Honors degree from IIT Kharagpur, where she was the first woman admitted to the Mechanical Engineering program.
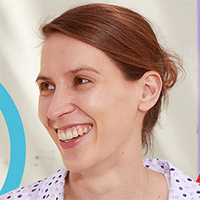
Dr. Mareike Kritzler is the Innovation Strategy Manager for the Simulation and Digital Twin Technology Field which has the goal to combine the physical and virtual world for industrial applications. Prior, she was the head of the Smart Machine Vision and Visualization team which focused on the human in the loop and allows for interaction with a Digital Twin or a physical machine through human-machine interfaces such as Augmented Reality. Mareike had the opportunity to join Siemens Corporate Technology in the Berkeley, CA, USA in 2014. Before that Mareike was a Development Specialist for Augmented Reality apps at a German startup, first in Munich, Germany and then in San Francisco, CA, USA. Her Diplom (M.S.) and PhD are in the field of Geoinformatics which were obtained from the University of Muenster where she worked as a student researcher and research assistant for several years.
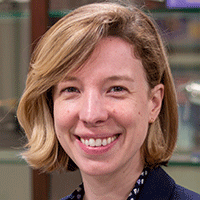
Dr. Astrid Layton is an associate professor and Donna Walker Faculty Fellow at Texas A&M University in the Mechanical Engineering department. She received her Ph.D. in Mechanical Engineering from the Georgia Institute of Technology and has a BS in Mechanical Engineering and Studio Arts from the University of Pittsburgh. Her research uses interdisciplinary collaborations to solve large-scale system problems, developing knowledge that supports designers and decision-makers. Dr. Layton is an expert on using biological inspiration for engineering systems design, with a focus on the use of biological ecosystems as quantitative inspiration for achieving sustainability and resilience in complex human networks. She is the recipient of several teaching and research awards including a 2024 National Science Foundation CAREER Award. She served as member and chair of ASME's Design Theory and Methodology's (DTM) technical committee, has been a guest editor for journal special issues covering resilient systems, networks & graphs, and sustainable design, and is currently an associate editor for ASME’s Journal of Mechanical Design.
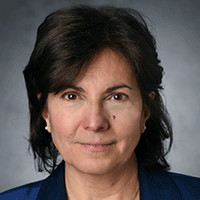
Dr. Janis Terpenny is a program director at the National Science Foundation (NSF) in engineering. She is also a professor of Mechanical Engineering and Systems Engineering & Operations Research at George Mason University. Her research focuses on smart integrated systems, processes for design and manufacturing, and engineering education. Her work has been supported by more than $16M in research funding and published in 200+ peer reviewed journal and conference papers. Previously, Janis served as Dean of Engineering at the University of Tennessee, department head at Penn State, department chair at Iowa State, director of the NSF Center for e-Design, program director for NSF’s Division of Undergraduate Education, and professor at Virginia Tech and the University of Massachusetts. She served as the first technology thrust lead for the Digital Manufacturing and Design Innovation Institute (DMDII), one of the nation’s first Manufacturing USA institutes (now MxD). She has industry work experience with General Electric (GE). She is fellow and member of ASEE, ASME and IISE, and member of AAAS, Alpha Pi Mu, INFORMS, SME, and Tau Beta Pi. She is a Governor on ASME’s Board of Governors. Janis has received awards for research and teaching innovation. She served as NSF Advance professor at Virginia Tech and has been an innovator and leader of many initiatives for the professional growth and success of women and other underrepresented groups in engineering.

I, Dr. Christine Toh, am an Assistant Professor in the Department of Engineering in the College of Integrated Science & Engineering at James Madison University. My research examines the design theories, methods, and approaches that form the basis of modern design endeavors in engineering and technology design. I study the influence of philosophical and intellectual traditions on the way that we make, research, think, and talk about our modern built world. Design is a negotiation between the forces that shape individuals, organizations, and societies, and I have dedicated my scholarship to understanding these forces and their interaction to get us one stop closer to fulfilling the design discipline's promise of improving society.
I teach in the Integrated Engineering program primarily focusing on the Design Methods and Process classes. As part of my goal of advancing the engineering design discipline, I also contribute to mentorship and community-building initiatives within the Design Engineering Division (DED) of the American Society of Mechanical Engineers (ASME).