Aerospace Electronics
Moderator: Dr. Ben Leever, US AFRL
Description: Flexible and printed electronics are providing new opportunities for aerospace electronics in terms of both innovative packaging solutions as well as unique form factors. Panelists will discuss packaging strategies to enable the integration of thin die as well as higher density electronic packages. They will also describe how flexible & conformal electronics (such as photovoltaics, antennas, and interconnects) deliver reduced weight and/or new capabilities for applications such as UAVs, satellites, and wearable sensors.
Panelists: Mary Herndon (Raytheon), Steve Gonya (Lockheed Martin), John Rogers (Boeing), David Shaddock (GE)
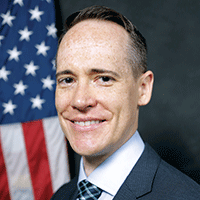
Moderator Biography: Benjamin Leever is currently the Technical Director in the Air Force Research Laboratory (AFRL) Manufacturing & Industrial Technology Division. As Tech Director, Dr. Leever is the principal advisor on internal & external technical programs for the division, and he functions as senior leader for the division addressing strategic planning & execution, definition of organizational & program policy, support for transition of technology, & establishment of appropriate partnerships with industrial customers.
Prior to assuming his current duties, Dr. Leever served as Government Chief Technology Officer of NextFlex, a $250M public-private partnership established to create a domestic manufacturing ecosystem in flexible hybrid electronics. He also previously served as the Advanced Development Leader for AFRL’s Soft Materials Branch, leading an external portfolio focused on flexible electronics and biomaterials. Prior to that role, he led a research team focused on the development and modeling of multifunctional materials for structural power applications. Dr. Leever earned a B.S. in Chemical Engineering from the University of Cincinnati and a Ph.D. in Materials Science & Engineering from Northwestern University.
Presentation Title: Printed and Flexible Electronics at Raytheon Technologies by Mary K. Herndon
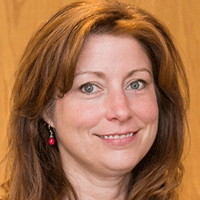
Presenter Biography: Mary K. Herndon is an Engineering Fellow on the Materials Engineering Technical Staff at Raytheon Missiles and Defense (RMD). Mary has a background in semiconductor physics, including processing and characterization of electronic materials.
Dr. Herndon joined Raytheon in January 2006 and was named Technology Area Lead for Mechanical, Materials and Structures in June 2014. In this role, she is responsible for technology planning and development for advanced materials and structures at RMD. Herndon works closely with universities and technology companies to implement next generation mechanical and materials technologies in Raytheon products. Mary is co-director of the Raytheon-UMass Lowell Research Institute (RURI), coordinating research on printed electronics and additive manufacturing for RF applications.
In 2017, Dr. Herndon was named Corporate Technology Champion for Mechanical, Materials and Structures. Reporting to the Corporate Vice President for Research and Innovation, the Technology Champions are responsible for providing long term shaping of corporate technology strategy across all business units within Raytheon Technologies.
During her tenure at Raytheon, Mary has implemented novel optical techniques for material characterization and served as a Materials Engineering lead for Zumwalt, Patriot and other programs. Mary has led multiple Advanced Materials and Innovation projects for Raytheon including sensor design for chemical and explosive detection, RF metamaterial research and development of printed electronics materials and processes.
Before joining Raytheon, she spent six years working at a start-up company, where she managed a silicon MEMS fabrication lab and specialized in transitioning electronic packaging processes to volume manufacturing. Mary received her Ph.D. in Applied Physics with an Emphasis in Materials Science from the Colorado School of Mines in December, 1999, working within the Center for Solar and Electronic Materials and collaboratively with partners at the National Renewable Energy Lab.
Presentation Title: Recent Advances in Additive Manufacturing for Electronic Packaging by John Rogers
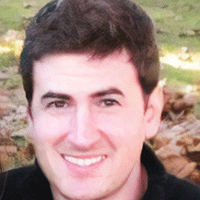
Presenter Biography: John Rogers is a Senior Electrical Engineer at Boeing's Research and Technology Division, Huntsville, AL. Prior to joining Boeing in 2017, he was an Electrical Engineer at Harris Corporation's Microelectronics Division, Melbourne, FL, from 2007 to 2013. He has a Ph.D. in electrical engineering from the University of Florida and was a corecipient of Boeing's Engineering Excellence Team of the Year in 2019.
Abstract: Today, we are living in a fourth industrial revolution where the things we interact with are becoming more autonomous. The Internet of Things (IoT) promises to improve the quality of life by bridging networks of sensors and devices. At the core of these sensors and devices are packaged electronics on printed circuit boards, which have not changed much in the past century. Additive manufacturing can fundamentally revolutionize the way circuit boards are manufactured. Recently, Boeing has been working towards maturing the manufacturability of multilayer flexible circuit boards including demonstrating an integrated printed antenna array operating in the X-band.
Presentation Title: Direct-Write Additively Printed Electronics for 3D RF Applications by Stephen Gonya
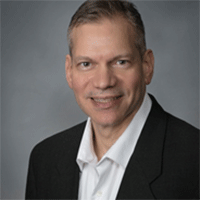
Presenter Biography: Responsible for new product designs, R&D, advanced manufacturing, quality assurance, failure analysis, reliability testing and materials consulting. Chartered to develop new and emerging technology for RMS next generation electronic platforms.
Current Research Activities:
- 3D conformal multi-layer circuitry over complex surfaces
- Direct-write printed electronics using additive manufacturing methods
- Printed 3D RF microwave circuit elements and antennas
- Flexible Hybrid Electronic (FHE) technology for UAV and EW platforms
- 3D-IC & 2.5D-IC chip stacking for system-in-package (SIP) applications
- Anti-Tamper volume protection and sensors for electronic hardware
Abstract: This topic focuses on leveraging industry/academia/government developed tools, materials, equipment and processes for direct-write (DW) printing and additive manufacturing (AM) to create electromagnetic (EM) circuit elements for radio frequency (RF) devices used in wireless communication, electronic warfare and radar systems. Our goal is to advanced fabrication technology for 3D-RF circuit elements using DW and AM methods. Direct-Write technologies enable the selective deposition and patterning of both dielectric and conductive material in a multi-layer fashion to create high-resolution 3D circuit elements on both flat and conformal surfaces. A hybrid circuit fabrication approach was chosen using conventional RF substrate materials and copper foil circuitry with Si and GaAs active die. Printed RF elements are placed in the circuit where there is a realizable advantage in terms of better performance, size reduction, lower cost, or faster build cycle. This new DW-AM technology for RF electronics is particularly relevant for millimeter-wave (mmW) and micro-wave (µW) systems. Aerosol Jet, inkjet, and extrusion DW methods are considered immediately relevant for hybridization with AM because they use digitally driven data from CAD files and afford multi-axis control of the deposition tool and multi-material delivery systems. Examples of printed RF elements being used for tech insertions include; CPWG transmission lines, bare die direct attach, coupling transformers, broadband bias inductors, limiter PIN diodes, MIS capacitor connections and various 3D or conformal antenna configurations.
Presentation Title: Additive Manufacturing for High Temperature Electronics Applications by David Shaddock
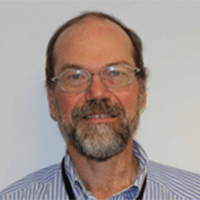
Presenter Biography: David Shaddock is a Senior Electronics Packaging Engineer at the General Electric Global Research. He received a B.S.M.E. degree from Carnegie-Mellon University and M.S.Eng. Sci. in Microelectronics Manufacturing from Rensselear Polytechnic Institute. His research interests are in harsh environment electronics, thermal management, electronics manufacturing and reliability. He has over 30 years of experience in electronics manufacturing and packaging at GE, Rockwell, and Motorola. He has over fifty-two (52) publications including thirty-three (33) in the field of high temperature electronics packaging and materials. Twenty-three (23) patents including nineteen (19) in the field of high temperature electronics, packaging, and sensors. He was a member of the Board of Advisors Association of Electronic Manufacturing, Society of Manufacturing Engineers 1999-2002, its chairman in 2002-2004, and was chairman of ASME E&PP High Temperature and Harsh Environment Electronics Committee in 2015.
Abstract: There is growing interest in applications for electronics in military and commercial aviation applications that can support mission needs to sense, actuate and communicate at temperatures beyond the normal range of operations. Electronics for extreme temperature environments has been demonstrated with SiC electronics to operate at more than 300 °C. Capability of electronics packaging materials and reliability at extreme temperatures has also been demonstrated in the temperature range of 300 to 750 °C using ceramic hybrid multi-chip modules technology but this approach typically requires high NRE costs and lead time. 3D additive processes reduce time and NRE cost for this packaging with the added benefits of novel 3D structures and embedded features. Additive manufacturing processes of metals, ceramics, conductors, and dielectrics provides a digital transformation of hybrid circuit manufacturing technology. However, understanding of additive pack-aging material properties and reliability at extreme temperatures is not known. The interest and investment at GE in both additive manufacturing and high temperature electronics supports this effort to develop and characterize materials and processes for additive fabrication of high temperature electronic packaging. An overview of the approach and accomplishments will be presented.
Printing Technologies for Additive Electronics
Moderator: Pradeep Lall, MacFarlane Endowed Distinguished Professor and Director, Auburn University
Description: Traditionally, electronics manufacturing has involved the use of subtractive processes requiring the use of plating, wet-etching, and masks. Additive processes hold the promise of a shorter time to first-prototype through the use of digitally-driven design and in some cases the added ability to migrate to non-planar structures. A number of processes have emerged for high volume production of electronics including aerosol-jet printing, ink-jet printing, direct-write and stencil printing. Each of the processes offers advantages with a balance of trade-offs in comparison with traditional methods. In this session, the panelists will provide an overview of each of the technologies and engage in discussion on the opportunities and the technology gaps related to each of the additive technologies.
Panelists: Bryan Germann (Optomec), Mike Newtown (nScrypt), Don Veri (SUSS), Doug Schardt (Komori America)
Moderator Biography: Professor Pradeep Lall is the MacFarlane Endowed Distinguished Professor with the Department of Mechanical Engineering and Director of the NSF-CAVE3 Electronics Research Center at Auburn University. He holds Joint Courtesy Appointments in the Department of Electrical and Computer Engineering and the Department of Finance. He is a member of the technical-council, academic co-lead of the asset-monitoring TWG, and past-member of governing council of NextFlex Manufacturing Institute. He is the author and co-author of 2-books, 14 book chapters, and over 650 journal and conference papers in the field of electronics reliability, safety, energy efficiency, and survivability. Dr. Lall is a fellow of the ASME, fellow of the IEEE, a Fellow of NextFlex Manufacturing Institute, and a Fellow of the Alabama Academy of Science. He is recipient of the Auburn Research and Economic Development Advisory Board Award for Advancement of Research and Scholarship Achievement, IEEE Sustained Outstanding Technical Contributions Award, National Science Foundation’s Alex Schwarzkopf Prize for Technology Innovation, Alabama Academy of Science’s Wright A. Gardner Award, IEEE Exceptional Technical Achievement Award, ASME-EPPD Applied Mechanics Award, SMTA’s Member of Technical Distinction Award, Auburn University’s Creative Research and Scholarship Award, SEC Faculty Achievement Award, Samuel Ginn College of Engineering Senior Faculty Research Award, Three-Motorola Outstanding Innovation Awards, Five-Motorola Engineering Awards, and over Thirty Best-Paper Awards at national and international conferences.
Presentation Title: High Performance & Reliable Aerosol Jet Printed 3D Interconnects for Bare Die & Components by Bryan German
Abstract: Flexible and wearable electronics have a wide range of applicability. Achieving flexibility on substrates like PET OR Polyimide sheet is straightforward and can be accomplished with many different printing techniques for high volume manufacturing processes. However, once unpackaged die or components are introduced to minimize size/weight of final devices and maintain flexibility things become more difficult. Traditional means for interconnecting die & components such as wire bonding are not able to be used as these de-packaged components have extremely small bond pads and bonding to printed metal on. As a result, a new method of interconnecting is required to create robust signal and power connections for the die to the circuitry around it. Aerosol Jet is a unique printed electronics technology which is able to create conductive printed 3D interconnects. These conformal electronic traces transfer signal and power into and out of the die similar to wire bonds but with lower profiles and the ability to interconnect to another printed circuitry. Several real-world examples are to be showcased along with reliability and signal performance, especially when signal frequencies climb over 40 GHz along with production-oriented equipment to deliver the solution to market.
Presenter Biography: Mr. Germann is product manager of the Aerosol Jet Product line, including machine platforms, print engine products, as well as digital and software products. He is also managing strategic customer projects centered around volume production applications for Aerosol Jet technology. Bryan joined Optomec in mid-2017, previously he worked for GE Power he successfully integrated Optomec’s Aerosol Jet technology into production work cells for printing high temperature ceramic sensors on heavy-duty gas turbine blades. His background in materials, process and Optomec’s core technology enable him to Optomec’s customer base working on high volume, production applications for Aerosol Jet. Bryan currently holds 13 published patents. He also holds a B.S. and M.S. in Mechanical Engineering from University of South Carolina (USC).
Presentation Title: Direct Digital Manufacturing – The Integration of Multi-material and Multi-processing by Mike Newton
Abstract: Direct Digital Manufacturing (DDM) has the potential to fabricate electrically functional complex shapes. Today electronics and electronic packaging is done using planar geometries. Extending to the 3rd dimension is done using wires, cables, connectors, bolts, and glue; this can be simply thought of as placing a square peg in a round hole. Making printed circuit boards into printed circuit cylinders or cones or other doubly curved shapes is not feasible using traditional PCB manufacturing methods. DDM is direct printing, milling, polishing, placing, curing, sintering, and monitoring on a single platform which provides the advantage of in situ processing and packaging capabilities for all stages of the manufacturing process. Next generation electronics will not be boards that are attached to objects, instead they will be objects with electronics permeating throughout the structure. The advantage of this is a reduction in wires, cables and connectors and the electronics can be more strategically placed therefore reducing the lengths of power lines. The net effect will be more efficient circuitry and ultimately more electronic functions per volume. A summary of DDM and working device demonstrations that are planar and non-planar will be presented. Additionally, questions of reliability, yield and throughput will also be addressed.
Presenter Biography: Mike Newton has 30+ years’ experience in the areas of advanced microelectronics and Microsystems technologies. He has built and managed a number of fabrication and research labs serving both commercial and government markets. Currently as nScrypt’s Director of Electronic Packaging developing total solutions in micro-dispensing and direct digital manufacturing for the electronic packaging market. Mr. Newton also serves as Strategic Technology and Transition Director with Sciperio, nScrypt’s parent company, leading strategic technology pursuits into the DoD, National Labs and DARPA. He currently has over 50 patents in advanced electronic packaging technologies. Mr. Newton’s interest includes serving as the Charter Organization Rep for Troop 37 and various K-12 educational and vocational outreach opportunities focused on STEAM.
Presentation Title: Printing 4.0 by Don Veri
Abstract: With the work of Gutenberg, printing technology enabled the mass manufacturing of books and other printed media. Today, printing technology spread beyond the graphical industry and plays a role in the manufacturing of many products, e.g. in electronics applications. In this presentation an update will be given of the role of inkjet printing in this landscape. We will show how the unique capabilities of inkjet printing qualify it for new ways of manufacturing. The benefits can be diverse and range from enabling things that were not easily possible before, to more basic effects such as decreasing cost through floor space, labour or waste management. Specific examples will be given for the manufacturing of solar cells, printed circuit boards and semiconductors.
Presenter Biography: Mr. Don Veri has an extensive international business development and sales background and has been active in the Semiconductor, Printed Electronics, Renewable Energy/Solar, and Technology/Process Automation market sectors for 30 years. He has held executive management and business/commercial development positions within industry leading companies including SUSS MicroTec and formerly with MBT System’s (a wholly owned subsidiary of Meyer Burger AG of Thun, Switzerland, Toolex USA/Toolex International, Smit Thermal Solutions and Metatec Corporation. Currently Mr. Veri is the Key Account/Business Development Manager for SUSS MicroTec’s, North American division. Mr. Veri has played an integral role in developing SUSS MicroTec’s Industrial Ink Jet Printing product lines for the Semiconductor, PCB, Printed Electronics and Photovoltaics markets. Mr. Veri has received his graduate (MBA) and undergraduate degrees (BS Natural Resources) from The Ohio State University.
Presentation Title: Seria Die Attach Solution for FHE Printing and Gravure Offset Equipment by Doug Schardt
Abstract: The presentation explains the equipment and techniques to reliably and repeatedly print traces down to 5 microns or less. The equipment highlighted is gravure offset (as opposed to gravure only). The machine shown is designed for small lot production or R&D although larger, more automated equipment is available for high production needs. Given the fine trace capability, next is a look at the strengths and weaknesses of different methods of chip mounting on fine printed circuits and how the same equipment can assist. Finally, the presentation will explore the use of gravure offset equipment to print a fanout pattern in combination with screen printing for the remainder of the product need.
Presenter Biography: Doug Schardt is Director of Product Management for Komori America including oversight of North American demonstration facility and national training. Technical knowledge includes sheetfed offset, web offset, digital, gravure, gravure offset, intaglio screen, flexo and various specialties. Application knowledge ranges through packaging, commercial, currency (banknote), pharma, and other unique markets. The Komori corporation leverages their broad base of experience and expertise gained from those diverse industries to bring to market an extraordinary lineup of equipment that takes printed electronics, both rigid and flexible to the next level. I am proud to be part of that advancement.
HIR Challenges and opportunities
Chair: Dr Gamal Refai-Ahmed, Xilinx Fellow
Co-Chair: Prof Leila Choobineh, Professor Sunypoly
Panelists: Prof Bahgat Sammakia (Vice President Binghamton University), Prof Amr Helmy (Professor University of Toronto), Dr. Ravi Mahajan ( Intel Fellow), Dr. Suresh Ramalingam(Xilinx Fellow)
Description: This panel will be addressing the challenges of the current and future HIR challenges. This is a complete dynamic panel. Panelists will be in a complete dialog with each other in the following areas:
- Can acadamia produce a valuable proposition to the industry
- Each academic panelist will give 1-2 examples
- Can Foundry provide a meaning information (i.e. manufacturing process, materials, assemble, analysis) to enable holistic Heterogonous Integration from Si supplier/OSAT/
- Each industrial panelist will give 1-2 examples
- Do we need to have a new definition of Life time in Heterogonous Integration era. h (i.e. Fit Budget should be done based on the end customer applications, Co-planarity should be revised in JEDEC, how can we connect TC (C/B/G..), Electro migration…. Component to system)
- Each Panelist will give its view
- What are the gaps from Panelists point view on the current offering road maps from HIR
Presenter Biographies:
Dr. Gamal Refai-Ahmed, Life Fellow ASME, Fellow Canadian Academy of Engineering, is a Distinguished Engineer and Adjunct Professor in Watson School of Engineering and Applied Science SUNY Binghamton. He obtained the M. A. SC. and PhD degrees in Mechanical Engineering from the University of Waterloo. He is the author of more than 90 technical papers and more than 100 US patents/International Patents/ Pending patents. He is an Associate Editor of Journal Components and Packaging, IEEE and Journal of thermal Sciences and Engineering and Applications, Transactions of the ASME.
Dr. Leila Choobineh is an assistant professor of Mechanical Engineering at SUNY Polytechnic institute. She received the Ph.D. degree (2014) in mechanical engineering from the University of Texas at Arlington. Her research interests include the development of micro- and nano-scale sensors, thermal management of 3D integrated circuits, microelectronics, flexible electronics, and microelectronics cooling. She recently received funding from Silicon Research Corporation and Research Foundation of State University of New York to work on nano porous metal applications for thermal capacitor and immersion cooling of microelectronics. She published her work at IEEE TCPMT, ASME Journal of electronics packaging, Applied Physics Letters, Applied Thermal Engineering, International Journal of Thermal Sciences and presented her work at ASME IMECE, ASME InterPACK, IEEE Itherm conferences. She is an Associate Editor of the IEEE Transactions on Components, Packaging and Manufacturing Technology journal. In addition, she had served as session chair, topic chair and track chair at IMECE, IEEE ITherm and ASME InterPACK conferences.
Bahgat Sammakia, a SUNY distinguished professor of mechanical engineering, is the vice president for research at Binghamton University.He is the founding director of S3IP, a New York State Center of Excellence, and is the director of the Energy-Efficient Electronic Systems Center (ES2) and the Center for Heterogeneous Integration Research in Packaging (CHIRP). Sammakia served as the interim president of SUNY Polytechnic Institute from December 2016 to June 2018. Sammakia, who holds 21 U.S. patents and has published more than 250 peer-reviewed technical papers, is a fellow of the American Society of Mechanical Engineers, the National Academy of Inventors, and the IEEE. He earned his bachelor's degree from the University of Alexandria in Egypt and his master's and doctoral degrees from the University at Buffalo. A former IBM senior technical staff member, Sammakia joined Binghamton University's faculty in 1998.
Amr S. Helmy joined the department of Electrical and Computer engineering of the University of Toronto with a mixed experience in academic as well as industrial settings. He received both his M.Sc. (1995) and Ph.D. (1999) degrees from the University of Glasgow, Scotland, in the field of photonics. Between 2000 and 2004 he joined Agilent Technologies, where he was involved in developing different photonic devices ranging from high reliability submarine-class lasers, to un-cooled single mode lasers, to integrated photonic circuits. Dr. Helmy’s research interests include quantum/non-linear integrated photonic devices/circuits and nano-photonic devices/circuits using hybrid metallic architectures. The application domains, where his group contributes, include optical signal processing, communications, and sensing.
Memberships/Awards
Vice President for the IEEE Photonics Society
Editor for several IEEE and OSA journals
Chaired flagship conferences for IEEE and OSA; namely CLEO and IEEE IPC
Ravi Mahajan is an Intel Fellow responsible for Assembly and Packaging Technology Pathfinding for future silicon nodes. Ravi joined Intel in 1992 after earning Ph.D. in Mechanical Engineering from Lehigh University. He holds the original patents for silicon bridges that became the foundation for Intel's EMIB technology. His early insights have also led to high-performance, cost-effective cooling solutions for high-end microprocessors and the proliferation of photo-mechanics techniques used for thermo-mechanical stress model validation. His contributions during his Intel career have earned him numerous industry honors, including the SRC’s 2015 Mahboob Khan Outstanding Industry Liaison Award, the 2016 THERMI Award from SEMITHERM, the 2016 Allan Kraus Thermal Management Medal & the 2018 InterPACK Achievement award from ASME, the 2019 “Outstanding Service and Leadership to the IEEE” Awards from IEEE Phoenix Section & Region 6 and most recently the 2020 Richard Chu ITherm Award For Excellence. He is one of the founding editors for the Intel Assembly and Test Technology Journal (IATTJ) and currently VP of Publications & Managing Editor-in-Chief of the IEEE Transactions of the CPMT. He has been long associated with ASME’s InterPACK conference and was Conference Co-Chair of the 2017 Conference. Ravi is a Fellow of two leading societies, ASME and IEEE.
Dr. Suresh Ramalingam graduated in 1994 with a Ph.D. in Chemical Engineering from Massachusetts Institute of Technology, Cambridge. He holds 32 US Patents, 2013 SEMI Award, Ross Freeman Award for Technical Innovation, ECTC 2011 Conference Best Paper Award, IMAPS 2013 and 2014 Conference Best Paper Awards for 2.5D/3D and book chapter on 3D Integration in VLSI Circuits. He started his career at Intel developing Organic Flip Chip Technology for Micro-processors which was implemented on Pentium II (Intel’s first flip chip product) in 1997. As one of the co-founders and Director of Packaging Materials at Scion Photonics he helped develop DWDM modules used by major communication companies. JDS Uniphase acquired Scion Photonics in 2002. As a Xilinx Fellow, he currently manages Advanced Packaging Interconnect Technology Development including TSV/3D for Xilinx FPGA products. Thermal Enablement and Board/System Level is a key focus area to push the power/performance envelope under the leadership of Dr. Gamal Refai-Ahmed and happy to be a partner in crime supporting the necessary technology pieces.
Women in Engineering
Tuesday, October 27, 2020
10:50am-12:50pm
Chair: Leila Choobineh
Panelists:
- Jelena Srebric, Professor, Acting Associate Dean of Research, A. James Clark School of Engineering, University of Maryland
- Anna M Prakash, Intel Corporation
- Nesrin Ozalp, Professor of Mechanical Engineering and Department Chair, Purdue University Northwest
- Elham Maghsoudi, NASA Jet Propulsion Laboratory
- Shelby Nelson, Mosaic Microsystems
- Tannaz Harirchian, Intel Corporation
Presenter Biographies
Dr. Leila Choobineh is an assistant professor of Mechanical Engineering at SUNY Polytechnic institute. She received the Ph.D. degree (2014) in mechanical engineering from the University of Texas at Arlington. Her research interests include the development of micro- and nano-scale sensors, thermal management of 3D integrated circuits, microelectronics, flexible electronics, and microelectronics cooling. She recently received funding from Silicon Research Corporation and Research Foundation of State University of New York to work on nano porous metal applications for thermal capacitor and immersion cooling of microelectronics. She published her work at IEEE TCPMT, ASME Journal of electronics packaging, Applied Physics Letters, Applied Thermal Engineering, International Journal of Thermal Sciences and presented her work at ASME IMECE, ASME InterPACK, IEEE Itherm conferences. She is an Associate Editor of the IEEE Transactions on Components, Packaging and Manufacturing Technology journal. In addition, she had served as session chair, topic chair and track chair at IMECE, IEEE ITherm and ASME InterPACK conferences.
Dr. Tannaz Harirchian is an engineering manager at Intel Corporation in Assembly & Test Technology Development organization. She leads a team of thermal mechanical engineers who are responsible for developing test capabilities and new technologies to enable testing of Intel products. Prior to her current role, she was a Packaging R&D Engineer where she led innovation and development of Intel CPU and SoC products with a focus on thermal-mechanical solutions for Mobile applications. She received her PhD in Mechanical Engineering from Purdue University in 2010. She has authored 1 book and more than 20 refereed journal articles and conference proceedings.”
Dr. Jelena Srebric is Acting Associate Dean of Research, A. James Clark School of Engineering and Professor, Director of CITY@UMD, Mechanical Engineering at Maryland Energy Innovation Institute. She received her Ph.D., in Building Technology at Massachusetts Institute for Technology in 2000, her Bachelor of Science, B.Sc. in 1994 and her Master of Science, M.Sc., in Mechanical Engineering at the University of Belgrade in 1997.
- Elected Fellow of the International Building Performance and Simulation Association (IBPSA) by the IBPSA Board, 2019
- Elected Fellow of the International Society of Indoor Air Quality and Climate (ISIAQ) by the Academy of Fellows of ISIAQ, 2018
- Inaugural Particle and Fibre Toxicology Prize Paper Award, 2016
- Serbian National Academy of Engineering, Elected International Member, 2013
- Outstanding Research Award, Penn State Engineering Alumni Society (PSEAS), 2012
Dr. Nesrin Ozalp is a Professor and Chair of Mechanical and Civil Engineering at Purdue University Northwest, and a Full Professor by Courtesy at the School of Mechanical Engineering of Purdue University West Lafayette. She received her Ph.D. from the University of Washington’s Mechanical Engineering Department and her MSc in Mechanical Engineering from Stanford University. Dr. Ozalp specializes in the areas of designing novel solar reactors for emission-free generation of fuels. She is the Lead Principal Investigator of research projects totaling $5M+, the corresponding author of 110+ peer reviewed journal, book chapter, and conference papers, Co-PI of completed Phase I of Solar Carbon Black commercialization with Fraunhofer, supervised 25 graduate students’ theses.
Dr. Elham Maghsoudi is a Thermal Engineer at NASA Jet Propulsion Laboratory (JPL) in the Propulsion, Thermal and Material Engineering section. She received her PhD in Thermo-fluid Science from Louisiana State University in 2013. She currently splits her time between thermal system engineering and management for Europa Clipper Magnetometer/Magboom and developing new thermal technologies for future JPL missions. Since joining JPL she has been completed the thermal design for the Psyche Magnetometer, performed Europa Lander exhaust plume analysis, developed novel 3D printed heat exchangers to support a variety of applications from an active thermally controlled CubeSat to actuators on a future icy moon robotic sampling arm.
Dr. Anna Prakash began her engineering career working on LCDs, HDTVs, and handheld communication devices. She joined Intel in 2004 as a Packaging R&D Engineer, focusing on automotive components & super computers. Anna has several patents & papers covering sensors and semiconductor packaging materials & process. Outside of work, Anna is passionate about promoting STEM education for local children. Along with her daughter Elaina, she co-founded Education Empowers Inc., a non-profit, to promote STEM education. Anna is the recipient of the 2019 Intel Hero award, Society of Women Engineers "Prism Award" and the IEEE STEM outreach award for her contribution to technology and the community.
Dr. Shelby F. Nelson is a semiconductor device physicist with broad industrial research experience. Her work has included ferroelectric materials at AT&T Bell Labs, silicon/germanium heterostructures at IBM’s Thomas J. Watson Research Center, and a mixed-signal CMOS process for ink-jet ejector heads at Xerox Corporation. In addition, Dr. Nelson spent 16 years as a Senior Research Scientist in the area of thin-film and printed electronics at the Kodak Research Labs.
Mobile, IOT and Computer Device Applications Panel: Thermal and Mechanical Challenges
Moderator: Dr. Victor Chiriac
Description: The emergence of 5G will help power a significant rise in mobile communication, IoT technology, providing the infrastructure needed to carry huge amounts of data, allowing for a smarter and more connected world – enabling Smart Cities, connected roads, advanced transportation (Self-driving cars), AR/VR, AI robotics, Digital healthcare, smart Sports and many other. Everything requires higher performance, more data, faster processors! Heterogeneous Computing involves the central processing units (CPUs), the graphics processing units (GPUs), high speed interconnects and other elements that push forward the computing industry. A panel of experts will share their vision on the future of small to large electronics thermal management and other advanced system level thermo-mechanical challenges and solutions of the future.
Panelists: Dr. Ravi Mahajan (Intel Corporation, Engineering Fellow), Mr. Hiroyuki Ryoson (Dexerials, Executive Chief Engineer), Professor John Thome (ex-EPFL, CTO of GCTG), Dr. Mark Earnshaw (Nokia Bell Labs, Group Lead/Director), Professor Amy Marconnet (Purdue), Don Le (Qualcomm, Principal Manager)
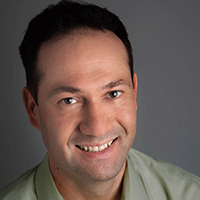
Moderator Biography: A Fellow of the American Society of Mechanical Engineers (ASME) since 2014, Dr. Victor Adrian Chiriac is a co-founder and a managing partner with the Global Cooling Technology Group. He previously held technology/engineering leadership roles, led corporate thermal technology teams and roadmaps, working on leading-edge mobile/wireless technologies with Motorola (1999-2010), Qualcomm (2010-2018) and Futurewei /Huawei R&D USA (2018-2019). Dr. Chiriac was elected Chair of the ASME K-16 Electronics Cooling Committee and was elected the Arizona and New Mexico IMAPS (International Microelectronics and Packaging Society) Chapter President in 2010. He is a co-editor of Electronics Cooling Magazine since 2016 and a leading member of the organizing committees of ASME/InterPack, ASME/ IMECE and IEEE/CPMT ITherm Conferences. He holds 19 U.S. issued patents, 1 US Trade Secret, 1 US Defensive Publication and has published over 109 papers in scientific journals and at international conferences. PhD (1999) in Aerospace and Mechanical Engineering, University of Arizona, Tucson, USA.
Presentation Title: Packaging Architectures for Heterogeneous Integration: Thermal/Thermo-Mechanical Implications by Dr. Ravi Mahajan
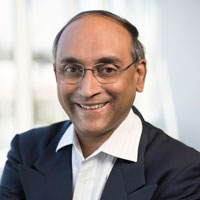
Presenter Biography: Ravi Mahajan is an Intel Fellow responsible for Assembly and Packaging Technology Pathfinding for future silicon nodes. Ravi joined Intel in 1992 after earning Ph.D. in Mechanical Engineering from Lehigh University. He holds the original patents for silicon bridges that became the foundation for Intel's EMIB technology. His early insights have also led to high-performance, cost-effective cooling solutions for high-end microprocessors and the proliferation of photo-mechanics techniques used for thermo-mechanical stress model validation. His contributions during his Intel career have earned him numerous industry honors, including the SRC’s 2015 Mahboob Khan Outstanding Industry Liaison Award, the 2016 THERMI Award from SEMITHERM, the 2016 Allan Kraus Thermal Management Medal & the 2018 InterPACK Achievement award from ASME, the 2019 “Outstanding Service and Leadership to the IEEE” Awards from IEEE Phoenix Section & Region 6 and most recently the 2020 Richard Chu ITherm Award For Excellence. He is one of the founding editors for the Intel Assembly and Test Technology Journal (IATTJ) and currently VP of Publications & Managing Editor-in-Chief of the IEEE Transactions of the CPMT. He has been long associated with ASME’s InterPACK conference and was Conference Co-Chair of the 2017 Conference. Ravi is a Fellow of two leading societies, ASME and IEEE.
Abstract: In this presentation, I will set the context for why Heterogeneous Integration using advanced packaging matters and briefly describe the various advanced packaging architectures in development. These architectures open up many challenges in thermal management and in ensuring robustness under thermo-mechanical stresses experienced during manufacturing and application conditions. I will describe how these challenges also offer opportunities for the packaging engineers in the fields of thermal management, reliability and thermo-mechanical analysis and experimentation.
Presentation Title: Packaging High Thermal Conductive EMI Shielding TIM by Mr. Hiroyuki Ryoson

Presenter Biography: Hiroyuki Ryoson finished the master’s degree in mechanical engineering at Kyoto University in 1990, and he joined Sony Corporation in 1990 and researched mainly in mechanical field. He is now an executive chief engineer in Dexerials Corporation (former Sony Chemical), and managing every theme in technology side in this company.
Abstract: In order to support 5G communication technology, it is necessary to perform large-scale information processing instantly, and it is expected that the heat density of LSIs will increase. At this time, heat dissipation from ICs such as CPU or GPU is a huge problem. Generally, the method of releasing heat from the IC to the heat sink is often used. However, since the heat sink is generally made of metal, the heat sink itself acts as an antenna and there is a risk that it emits an electromagnetic field due to electromagnetic coupling between the heatsink and the IC. In order to suppress such a phenomenon, a new type TIM In which carbon fibers are oriented in thickness direction is developed which has two performances in one material, which performances are EMI shielding performance and high thermal conductivity. And this material can achieve a high thermal conductivity of 20 W/mK.
Presentation Title: Cooling of Mobile and Portable Electronics with Pulsating Heat Pipes by Professor John R. Thome
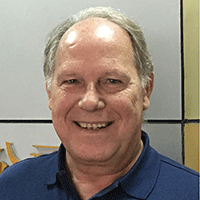
Presenter Biography: Technical Director of Global Cooling Technology Group in Phoenix, AZ developing pulsating heat pipe technologies for the mobile electronics market as well as JJ Cooling Innovation in Lausanne, Switzerland, a micro-two-phase cooling technology development company for numerous other industries. Has 20+ years of experience with development of micro-two-phase cooling systems for electronics (pumped systems, thermosyphons and pulsating heat pipes and high-fidelity simulators for them). Is the author of five books and is editor-in-chief of the Encyclopedia of Two-Phase Heat Transfer and Flow (16 volumes). He received the 2017 Nusselt-Reynolds Prize, the 2019 IEEE ITHERM Award and the 2019 ASME InterPACK Medal, the ASME Heat Transfer Division's Journal of Heat Transfer Best Paper Award in 1998, the UK’s Institute of Refrigeration J.E. Hall Gold Medal in 2008, the 2010 ASME Heat Transfer Memorial Award, among others.
Abstract: Pulsating heat pipes (PHPs) are an emerging two-phase cooling technology for cooling of mobile and portable electronics. A PHP consists of a serpentine channel that runs back-and-forth from the hot end (cooling electronics) to the cold end within a thin plate. The two-phase flow inside the serpentine is designed to be inherently unstable, with bubbles growing in the evaporator zone and condensing in the cold zone, and by transporting latent and sensible heat from the hot end to the cold end is able to cool devices with moderate up to high heat loads with a very thin shape factor. PHPs are particularly effective as they can operate in any orientation and can transport heat to large cooling surface areas. Innovative PHP studies of Global Cooling Technology Group and related thermal performance results will be presented together with prospects for future applications.
Presentation Title: Thermal Challenges in the New 5G End-End Network Era by Dr. Mark Earnshaw
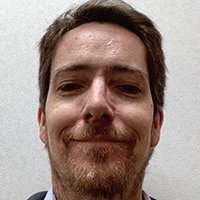
Presenter Biography: Dr. Mark and optical transceivers. His recent work has focused on developing a hybrid photonics integration platform for extremely efficient optical communications and sensing applications. Mark Earnshaw has received the Bell Labs President’s award and Bell Labs & CTO award and the 2018 Nokia US Top Inventor Recognition Award.
Abstract: The new 5G era will impact all aspects of communication networks including not just radio antennas but the access network and edge data centers which will create seamless connectivity to enable the new era of industrial automation. The new services will drive capacity growth both directly but also indirectly in order to achieve the new ultra-low latency and ultra-high reliability demands. Massive MIMO antenna arrays have clear need for advances in efficient, lightweight cooling solutions. Optical transceivers interconnecting antennas to remote radio access network equipment and edge cloud data centers are reaching extremely high-power densities. The harsh operating environments in which networking equipment is often deployed require novel device and system level reliability solutions for mission critical end-to-end connected services to be viable.
Presentation Title: Engineering Materials for Thermal Challenges by Professor Amy Marconnet
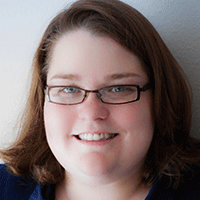
Presenter Biography: Amy Marconnet is an associate professor of Mechanical Engineering at Purdue. Research in the Marconnet Thermal and Energy Conversion (MTEC) Lab intersects heat transfer, energy conversion, and materials science to enable advances in technologies where energy conversion and thermal transport are key factors in performance. Prof. Marconnet has developed an interdisciplinary research program to evaluate, understand, and control the physical mechanisms governing the multi-functional properties of materials, machines, and systems. Recently, Dr. Marconnet won the 2020 Bergles-Rohsenow Young Investigator Award in Heat Transfer from ASME.
Abstract: Mobile platforms, IoT, and compute devices with limited heat dissipation pathways are becoming ubiquitous while requiring integration of dissimilar materials and components with a high density of interfaces and placing additional constraints on device performance. Open challenges exist in optimizing and tuning the thermal transport within the multi-scale materials in these heterogeneous systems, while meeting constraints on mechanical properties and device performance. Ultimately, efficient, thermally informed engineering is needed to translate research into technology and requires integrated modeling, experiments, and materials development.
Presentation Title: Thermal Design Challenges & Possible Solutions in 5G Mobile/Wireless Devices by Don Le
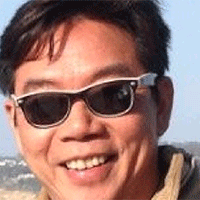
Presenter Biography: Don Le is a 25-year veteran of the semiconductor/computer product development industry. His work included thermal solution development for CPU, GPU, and mobile SOC from silicon/package to system levels at IBM, Intel, Nvidia, and Qualcomm.
Abstract: As 5G technology becomes more prevalent on various mobile wireless devices along with increasing demand for higher performance, the author will outline some of the challenges and thermal solution techniques that can be employed to optimize the performance of the products.
Advances in Wearable/Wireless Flexible Electronics: Thermal and Mechanical Challenges and Opportunities
Moderator: Dr. Victor Chiriac
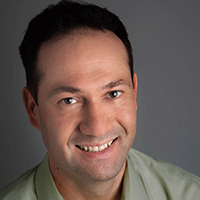
Moderator: Dr. Victor Chiriac, Managing Leader of Global Cooling Technology Group, ASME Fellow
Summary: The emergence of 5G will help power a significant rise in wearable/mobile/wireless communication, providing the infrastructure needed to carry huge amounts of data, allowing for a smarter and more connected world. A panel of experts from diverse industrial sectors and academia will share their vision on the future of small to large wearable/wireless flexible electronics thermal management and other advanced system-level thermo-mechanical challenges and solutions of the future.
Panelists: Dr. Kinzy Jones, Jr. (Magic Leap, VP Engineering), Professor YC Lee (UC Boulder, CEO of Kelvin Tech), Matthew Dalton (WP-AFRL, Engineering Lead), Prof Amy Marconnet, (Purdue), Dr. Luca Amalfi (Nokia/Bell Labs, Sr Engineer)
Presentation Title: User-Centric Modeling in Spatial Computing by Kinzy Jones, PhD
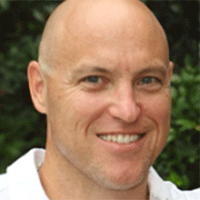
Presenter Biography: Dr. Jones' background is mathematical modeling including materials, fluids, and structures. His work, and that of his team, strives to use simulation, material analysis, and high fidelity testing to predict product failures and identify design improvements, thus reducing cost from unnecessary prototype builds and field failures, reducing time to market, and improving KPIs. He has been at Magic Leap for six years creating and managing the Advanced Mechanics and Materials group and serving as a Magic Leap Fellow. Previously, he was a Distinguished Member of the Technical Staff at Motorola and Vice President of Consulting Services at Amoeba Technologies. He received his Ph.D. from the University of California, Berkeley in Materials Science and Engineering in 1999.
Abstract: Spatial computing facilitates mixed reality experiences and is poised to become the world’s next computing platform. This will enable innovative forms of entertainment, productivity, education, communication, and commerce. This new platform will radically change human interaction with technology by blurring the lines between the physical and virtual worlds – making computer interaction richer, faster, and more enjoyable. The addition of 5G will further this merging, enabling virtual objects to 'live' in our physical environments just as physical objects do today. Achieving this grand vision requires overcoming many challenges. This talk focuses on moving from device- to human-centric metrics and results. Traditional device-centric key performance indicators (KPI) like temperature, stress, and displacement, are difficult to resolve in terms of user experience, potentially focusing engineering effort on parameters with limited impact. This talk presents two examples showing a user-based, rather than device-based, approach to spatial computing product development: human thermal comfort modeling, and the use of multiphysics to determine sensor performance.
Presentation Title: Flexible Thermal Ground Planes for Smartphones, Computers and Power Electronics by Dr. Y. C. Lee
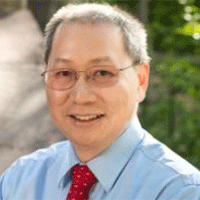
Presenter Biography: Dr. Y. C. Lee is the President and CEO of Kelvin Thermal and Professor of Mechanical Engineering at the University of Colorado Boulder. Dr. Lee received the ASME InterPACK Achievement Award in 2013. He was the Editor of ASME Journal of Electronic Packaging from 2015 to 2020.
Abstract: Flexible thermal ground planes (TGPs) are vapor chambers designed and manufactured using flexible circuit board technologies. The first TGP product is to be mass produced by 4Q in 2020. Our TGP is known for its outstanding features: thinnest configuration, large size, flexible, conformable, deformable, foldable, super isothermal, high heat flux and low cost. Kelvin Thermal is well positioned to provide leading thermal management solutions for smartphones, tablets, laptop computers, ARs/VRs, displays, electric vehicles with autonomous features, GaN-based power electronics, and edge and cloud computing. This brief presentation will illustrate some of the TGP products to be introduced in the near future: 0.150mm TGP, polymer TGP, folding TGP and high power TGP.
Presentation Title: SmartMedTech Prototype Wearable Devices for the USAF Aeromedical Mission by Matthew Dalton
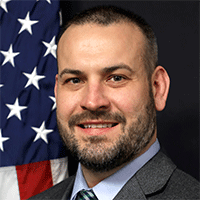
Presenter Biography: Matthew J. Dalton is a Research Chemist and Program Manager within the Soft Matter Materials Branch of the Materials and Manufacturing Directorate at the Air Force Research Laboratory. Executes the branch’s applied technology development portfolio developing and demonstrating advanced materials solutions for aerospace wearable technology for both the high performance flight environment and the aeromedical mission. Manages the Materials for Aeromedical Technology and Care Program developing low-cost physiological sensors for the En Route Care mission. Mr. Dalton obtained his BS in Chemistry from Wright State University and his MS in Materials Chemistry from the University of Illinois at Urbana-Champaign.
Abstract: The En Route Care (ERC) Aeromedical Evacuation (AE) system provides for the strategic military medical evacuation of patients and wounded warfighters. Vital to this mission is the pursuit of new methods for transporting patients with increased effectiveness and efficiency while dealing with the unique challenges of the aerospace transport environment: reduced barometric pressure and oxygen availability, increased accelerational and vibrational forces, ambient thermal instability, and a dry environment that may negatively impact patient health or device performance during transport. Reliable, wireless, wearable physiological monitoring technology can help the AE medical provider optimize patient care en-route through increased situational awareness, alerting, and decision support. Most commercial off-the-shelf (COTS) technology does not meet USAF or military requirements (JECETS, MIL-STD-810H) for operational use. Flexible electronic prototypes in development and challenges and opportunities will be discussed.
Presentation Title: Flexible, High Thermal Conductivity Materials by Professor Amy Marconnet
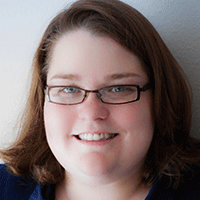
Presenter Biography: Amy Marconnet is an associate professor of Mechanical Engineering at Purdue University. Research in the Marconnet Thermal and Energy Conversion (MTEC) Lab intersects heat transfer, energy conversion, and materials science to enable advances in technologies where energy conversion and thermal transport are key factors in performance. Prof. Marconnet has developed an interdisciplinary research program to evaluate, understand, and control the physical mechanisms governing the multifunctional properties of materials, machines, and systems. Recently, Dr. Marconnet won the 2020 Bergles-Rohsenow Young Investigator Award in Heat Transfer from ASME.
Abstract: The emergence of wearable and flexible electronics necessitates the development of flexible materials with tailored thermal/mechanical properties not naturally occurring. A particular challenge for wearable electronics is optimizing and tuning the thermal transport to dissipate heat to the environment without exceeding safety limits for human contact and while maintaining the mechanical flexibility for user comfort. Woven materials consisting of high thermal conductivity fibers have shown significant promise in meeting these multi-functional needs. From a filament to fabric perspective, we have developed new metrology tools to evaluate these systems and provide feedback as we engineering high thermal conductivity, flexible materials for wearable and flexible electronics.
Presenter Title: Mini-Pulsating Heat Pipes for Wearable and Flexible Electronics by Dr. Luca Amalfi
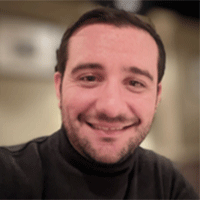
Presenter Biography: Raffaele Luca Amalfi is a Member of Technical Staff and Lead Researcher at Nokia Bell Labs New Jersey, where he performs cutting-edge research in the field of thermal management of high-performance telecommunications and computing systems across multiple scales. He is the Principal Investigator on behalf of Nokia of America Corporation and Bell Labs for the Eurostars Project PCOOLDATA focused on the development of innovative cooling solutions for datacenters. His research activities include: macro-to-micro-scale heat and mass transfer, thermal-mechanical design of advanced heat exchangers, integrated opto-electronics thermal management; active and passive thermal solutions for electronics, power-electronics- and datacenter-cooling. He has received a Ph.D. in Energy Engineering from EPFL and he has authored more than 30 scientific publications.
Abstract: The world is entering the Fourth Industrial Revolution that is bringing together digital, physical, and biological systems, which will deeply transform economy and society. Demand for processing, transporting, and storing digital data is growing exponentially, and this will have profound implications on system design with the associated trend toward achieving greater device functionality per unit volume. Sensing and diagnostic wearable devices, as well as flexible electronics are seen as emerging products, allowing greater connectivity between humans and machines. However, these devices present many thermal and mechanical challenges. Embedded passive two-phase cooling represents a viable and attractive solution, as it provides high heat dissipations and uniform heat spreading coupled with small form factors. In this talk, I will discuss the benefits and opportunities of implementing mini-pulsating heat pipes to keep scaling and developing advanced wearable and flexible devices.
Potential of Additive Manufacturing for Power Electronics Panel
Panelists: Charles Lents (RTX), G.Q. Lu (Virginia Tech), Michael Fish (Army Research Laboratory), Peter DeBock (DOE)
Presentation Title: Rethinking Power Electronic Packaging: Multifunctional Components and Transient Mitigation by Dr. Michael Fish & Dr. Peter de Bock
Abstract: Incredible improvements in power electronic devices have been accompanied by only incremental advances in the packaging technologies that support them. The capabilities of wide bandgap materials are not fully realized because they are held back by traditional module architectures that ultimately limit the power density of power conversion systems. I will discuss recent efforts at ARL and at Academic and Industry partners that explore novel components, materials, and approaches to electrical-thermal co-design. Areas where additive manufacturing can enable the realization of these approaches will be highlighted, and gaps where further development is necessary will be discussed.
Presenter Bio: Dr. Michael Fish is a research scientist at the Advanced Power Packaging group at the U.S. Army Research Laboratory, where he serves as Principle Investigator for the Thermally Enabling Architectures for Pulsed Power Systems (TEAPPS) tri-service program. His current interest is in the packaging and management of highly transient electronic systems, with particular focus on directed energy systems, vehicle electrification, and power conversion. He is one of three primary developers of ARL’s open source thermal-mechanical co-design and simulation tool, ARL ParaPower.
Presenter Bio: Dr. Peter de Bock currently serves as Program Director at the Advanced Research Projects Agency-Energy. His focus at ARPA-E includes electronics thermal management and aviation propulsion systems. Prior to joining ARPA-E, Dr. de Bock spent nearly 18 years with GE Research, holding various research and development positions and recently completing a focus on a system perspective on electrification of aviation. At GE Research, Dr. de Bock served as a Principal Engineer and Platform Leader for Power and Thermal Management Systems, and principal investigator on advanced programs in the areas of additive heat exchangers and advanced propulsions systems. Dr. de Bock also serves as the chair of the ASME K-16 committee on Heat Transfer in Electronics equipment and holds about 40 patents. Raised in the Netherlands, Dr. de Bock received his Ph.D. in Mechanical Engineering from the University of Cincinnati and holds degrees from academic institutions in the Netherlands, US and the UK.
Title: Opportunities and Challenges for Additive Manufacturing of Power Electronics Magnetics by Dr. Guo-Quan
Abstract: Inductors and transformers are necessary components for converting electric and magnetic energy in switch-mode power electronics (PE) systems. The process of designing and selecting a magnetic component, namely its core material and winding structure, is a critical task faced by a PE engineer for achieving higher conversion efficiency and power density. Today, a PE designer relies on standard sets of commercial magnetic cores with limited selections of core materials, shapes, and form factors. This limitation has prevented the engineers from implementing innovative designs of the components that would lead to improved performance metrics. Given its advantages of rapid prototyping and flexibility in making complex structures, additive manufacturing could be an ideal tool to make custom-designed magnetic components. However, the fact that an inductor or transformer is made of at least two types of materials, magnetic for the core and metal for the winding, presents significant challenges to 3D-printing the components. Of the many challenges, the most difficult one has to do with material feedstock. In this presentation, I will share our work on processing and demonstration of magnetic paste materials as feedstock to a multi-extruder 3D printer for making custom inductors. Barriers to further advance the manufacturing technology in the PE field will be discussed.
Presenter Bio: Dr. Guo-Quan (GQ) Lu is a professor jointly appointed between the Department of MSE and the Bradley Department of ECE at Virginia Tech. He has a double-major BS degree in Physics and MSE from Carnegie-Mellon University and a PhD degree in Applied Physics/Materials Science from Harvard University. He worked briefly at Alcoa Technical Center before joining Virginia Tech. For over 25 years of his professional career, Dr. Lu has researched on: packaging and integration of power electronics; three-dimensional, double-side cooled power modules; silver sintering for bonding power semiconductor devices; and recently magnetic materials for additive manufacturing of power magnetics. Dr. Lu has a Virginia Tech teaching award and a National Science Foundation CAREER award. His development of a die-attach nanoscale silver paste was recognized by an R&D 100 award. He has published over 170 peer-reviewed journal articles. Dr. Lu is an IEEE fellow.
Title: Electrified Propulsion Thermal Challenges by Mr. Charles Lents
Presenter Bio: Mr. Lents has over thirty five years of experience in the conceptual design of integrated aircraft primary and secondary power and thermal management systems. Mr. Lents is responsible for integrated aircraft systems, thermal management, and innovative propulsion systems technology development, and currently leads the Raytheon Technologies Research Center Electrified Propulsion research focus area. Mr. Lents received his B.S. in Mechanical Engineering from the University of Illinois and his M.S. in Mechanical Engineering from Purdue University.